Trust RME to raise the standard
WE ARE RME
RME is the world's most trusted original equipment manufacturer (OEM) of mill relining technologies. Our mission is to reduce hazardous risk and improve the availability of mineral concentrators.
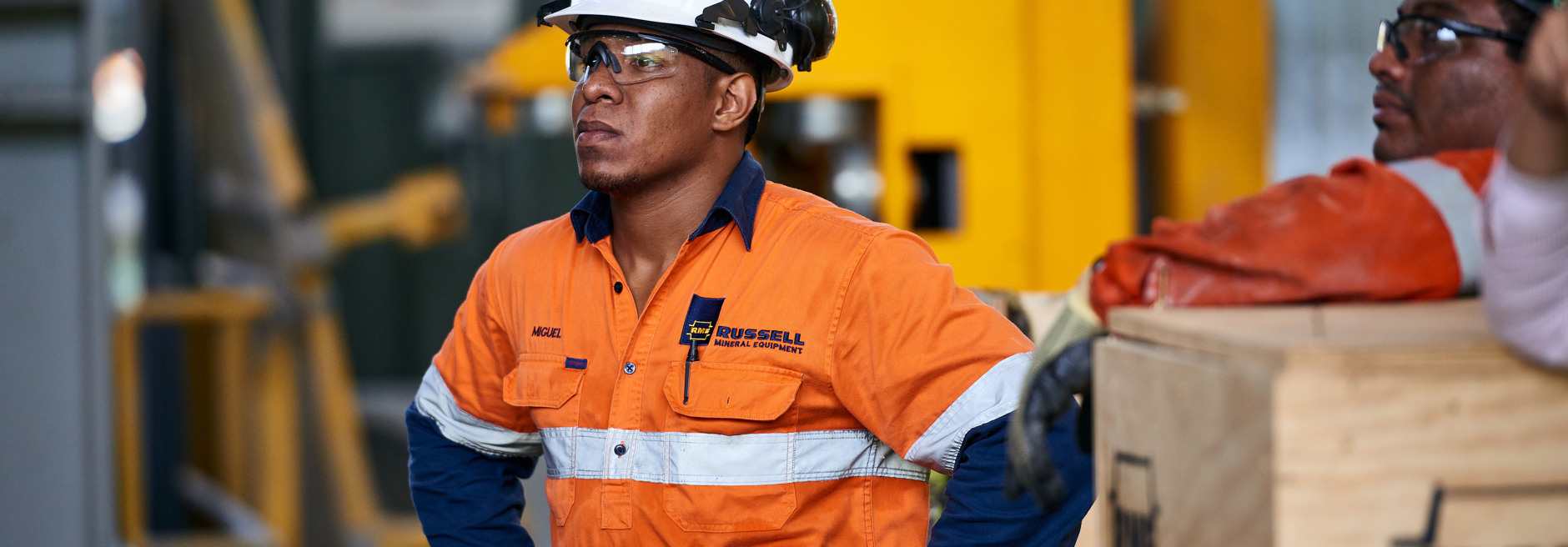
Persistent innovation and enduring commitment
For 40 years RME has dedicated itself to serving the comminution industry. Our innovative solutions help our Customers eliminate hazardous risk and improve mill availability through safe, fast, reliable relines.
A noble purpose, no doubt. But who we are, is far more humble. Ours is a story of many, many steps that have then delivered leaps in safety and productivity. A story of persistent innovation and enduring commitment to our people, Customers and planet.
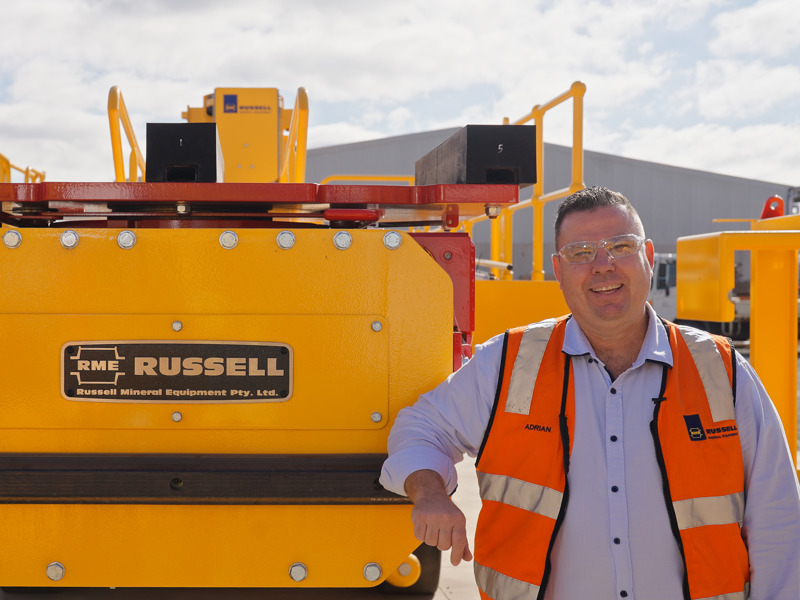
For our industry. For our planet.
RME aspires to improve the human condition through responsible access to metals at lower cost.
It’s an aspiration that sees us charged with the responsibility of our people and Customers’ safety and wellbeing. And in the race to a carbon neutral future, it sees us charged with the responsibility of enhancing our Customers' ability to meet the growing demand for minerals, like copper, necessary for the energy transition.
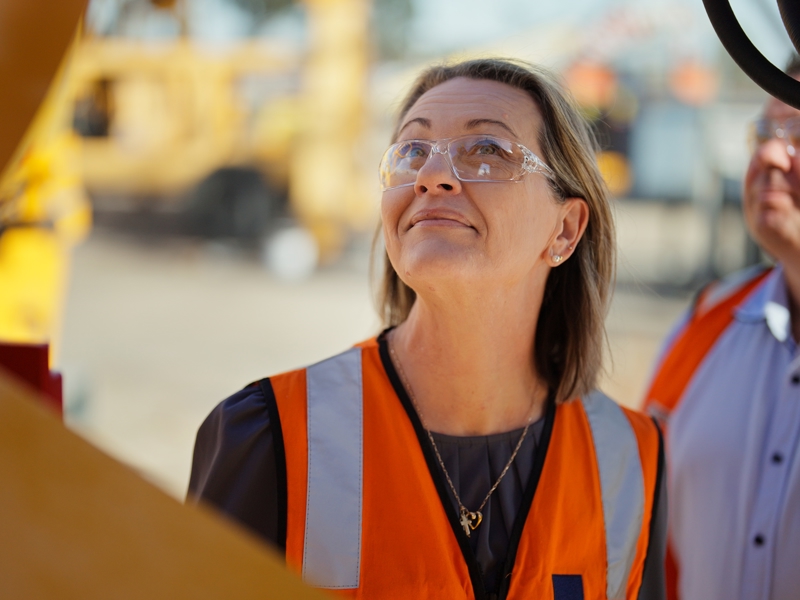
RME'S INTEGRITY SETS IT APART
Fast
Leveraging verifiable, time-tested and cutting-edge technologies, systems engineering, progressive implementations and close collaboration with reline crews, we enable our Customers to achieve consistently faster relines and higher mill availability.
Reliable
To keep mills running smoothly, our durable technology solutions are built to last, and are supported by our skilled and dependable technicians. Our modular and future-proofed technology ecosystem means we can offer upgrades for enhanced performance.
Safe
In partnership with our Customers, we have set new industry-wide safety standards by mechanising hazardous, highly-fatiguing manual handling tasks. With safety continuing to drive our technology evolution, and through automation, we are now enabling liner exchange to be performed safer and faster from outside the mill. Upgrades, repairs and accessories maintain asset performance, further reducing safety risks.
OUR FLAG ON THE HILL
At RME, our values reflect the culture we encourage and celebrate, and the experience we are creating for our people and Customers.
Safety
Since 1985, RME dedicated itself to the task of improving safety. This task remains core to our mission and purpose, and will continue to drive our technology innovation and support services.
Trust
Integrity is the quality of being honest and having strong moral principles, making us trustworthy. Our Customers understand that at RME, quality is never compromised, and takes priority over delivery and profitability.
Innovation
We understand that innovation is crucial to continuing our organisation’s and Customers’ success. At RME, we constantly challenge the status quo, creating new and better ways for RME and our Customers to be successful.
Accountability
We believe accountability promotes efficiency and harmony. We take responsibility and ownership of our decisions, actions, performance and behaviour.
Reliability
Reliability is a defining characteristic of RME and sets us apart from the crowd. Our colleagues and Customers depend on us to get it right, consistently. Downtime is costly, and fatal risk is unthinkable.
Longevity
At RME, we consider the long-term impact of our decisions on our colleagues, Customers, industry and community. This in turn helps to ensure our purpose and values continue, perpetually.
DEEP LOCAL ROOTS AND GLOBAL REACH
When John Russell founded RME in 1985 in Toowoomba, Queensland, he set out to mechanise the mill relining process to improve safety, shorten reline times and increase mine site profitability. Today, RME is the world's most trusted original equipment manufacturer of mill relining technologies.
With the support of a dedicated and highly skilled team, loyal and forward-thinking Customers, and dependable suppliers, RME has grown to operate in 64 countries, with 12 international Sales and Service Centres, employing more than 450 people worldwide. There are more than 440 mine sites across the planet served by RME’s equipment and services, including more than 570 RUSSELL Mill Relining Machines.
“Since 1985, RME has innovated mill relining technologies and services with an unwavering commitment to: improving the safety and productivity of our Customers’ operations and the safety and development of our people, the creation of local jobs, supporting Australia’s sovereign industrial capabilities, and bettering the communities in which we operate.”
FROM SMALL STEPS TO GIANT LEAPS. RME's 40 YEARS OF INNOVATION.
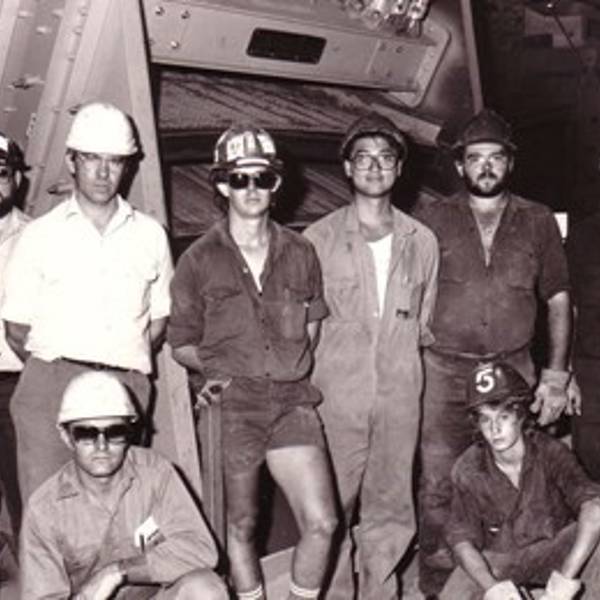
Early 1980s
The formative years
As a graduate mechanical engineer at Mount Isa Mines, John Russell saw first-hand how replacing grinding mill liners was a dangerous and time consuming activity that impacted plant availability.

1985
A vision to mechanise mill relining
RME was established with the vision to mechanise the mill relining process, shorten reline times, and improve concentrator availability and profitability—all while improving the safety of the work environment for reline crews.
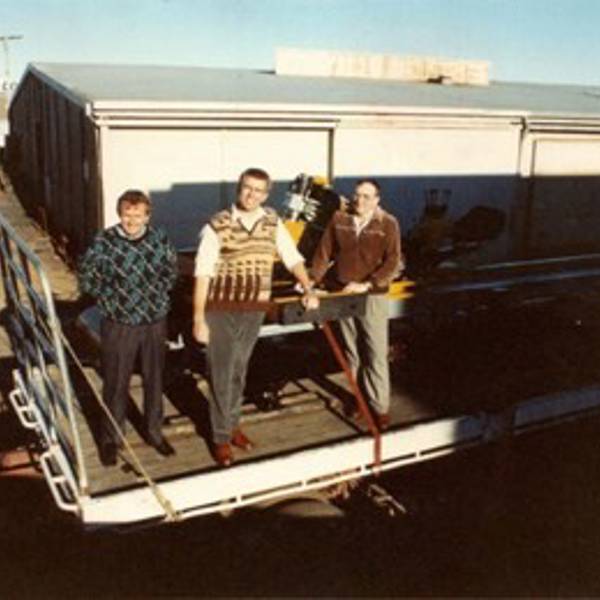
1990
The hard work started paying off
The hard work started paying off, and RME was now a team of three: two mechanical engineers, John Russel and Peter Rubie, and draftsperson, Doug Neild.

1990
The world's first mill relining machine
RME’s first RUSSELL Mill Relining Machine (MRM), a RUSSELL 6, was commissioned by Mount Isa Mines (MIM) for its lead zinc concentrator rod mills. As a result, relining times for the rod mills dropped from 44 hours to 24 hours—two 12 hour shifts.
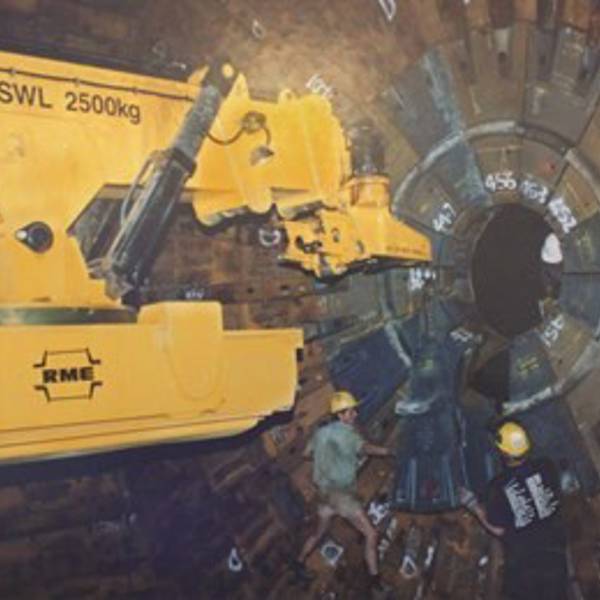
1991
World's first 7-axis mill relining machine
In a pioneering move, RME was chosen to design and supply a 7-axis MRM to a new Leinster Nickel Project in Western Australia. It was the first large-capacity liner-placement machine in the world capable of lifting 2500kg liners. Affectionately nicknamed "MRM No. 2," this inaugural RUSSELL 7 faithfully served the site's 32 ft SAG mill for over 30 years before being replaced with a new RUSSELL 7 in 2023.
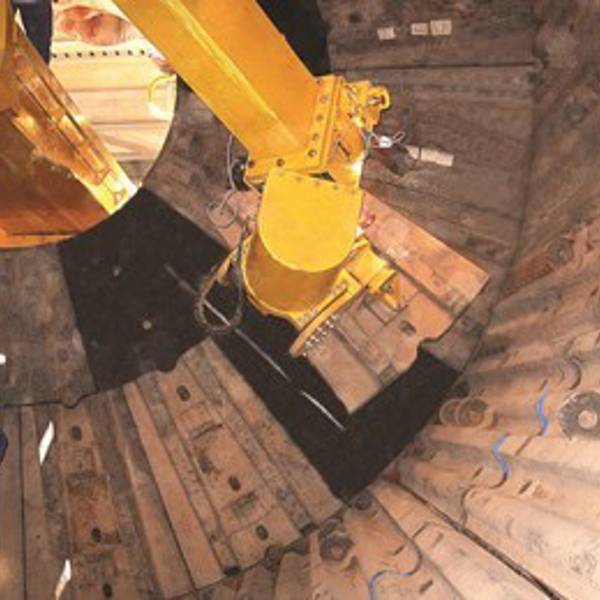
Early to mid 1990s
RME's global impact becoming evident
It was clear that RUSSELL MRMs were enabling the transformation of the mineral processing industry. Their ability to mechanically manipulate liners overcame manual handling limitations, allowing larger but fewer pieces to be used, which reduced reline times. This also paved the way for larger SAG mills, which were built to suit the largest RUSSELL MRMs at the time.

1995
Solving the worn liner removal problem
As mill liners became larger, removing them became harder due to issues like liner and liner bolt peening. While RME had a solution for liner handling, the industry needed to solve the worn liner removal problem—it needed a powerful recoilless hydraulic hammer purpose-built for the knock-in phase of mill relining. In 1995, RME lodged a patent for the Linerbolt Removal Tool, also referred to as the LRT at the time, co-invented by John Russell and Peter Rubie.
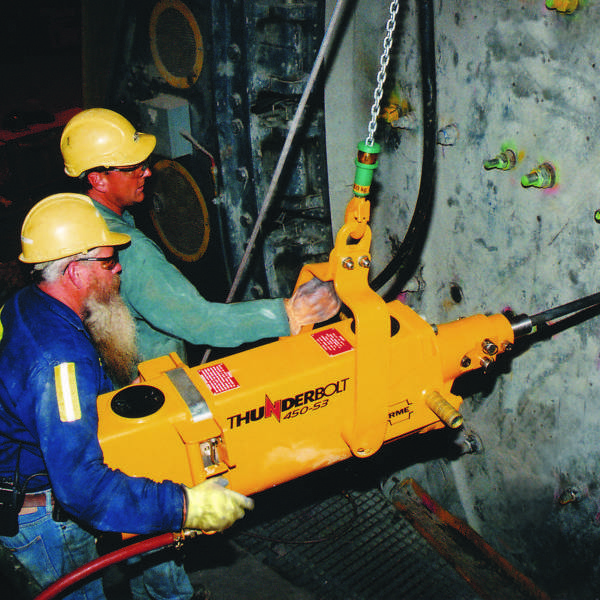
1997
THUNDERBOLT Recoilless Hammer
If RUSSELL 7s made mill relining good, the new THUNDERBOLT Recoilless Hammer, made mill relining great. It profoundly revolutionised worn liner removal. The combination of THUNDERBOLT Recoilless Hammers and the RUSSELL 7 MRM working in unison secured the foundation for the RME Mill Relining System. Crews now had the tools to slash traditional grinding mill relining times even further—without compromising safety.
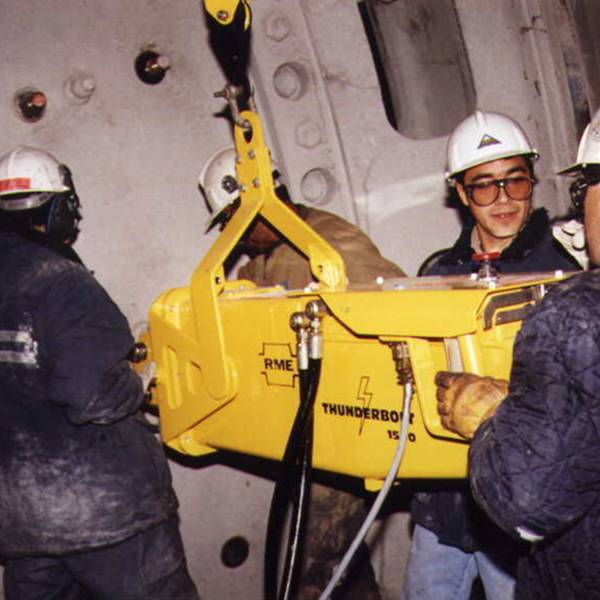
1999
Engineered for Impact: The 1500 Joule Advantage
BHP's Minera Escondida copper mine in Chile commissioned a larger THUNDERBOLT Recoilless Hammer, now known as the THUNDERBOLT 1500 Special Performance Recoilless Hammer. Even the toughest SAG mill discharge-end bolts met their match against the relentless force of this mighty hammer. Packing a consistent 1500 joules of energy at 55-60 blows per minute, it made shorter work of any knock-in challenge.

2000
Addressing every step, from ‘feed-off’ to ‘feed-on’
With the combination of the THUNDERBOLT Recoilless Hammers and the RUSSELL 7 MRM forming the foundation of the RME Mill Relining System, RME was now working to improve every step on the mill relining path to optimise mill availability. This period saw the development of RUSSELL Feed Chute Transporters (FCTs) for the removal and transport of mill feed chutes.
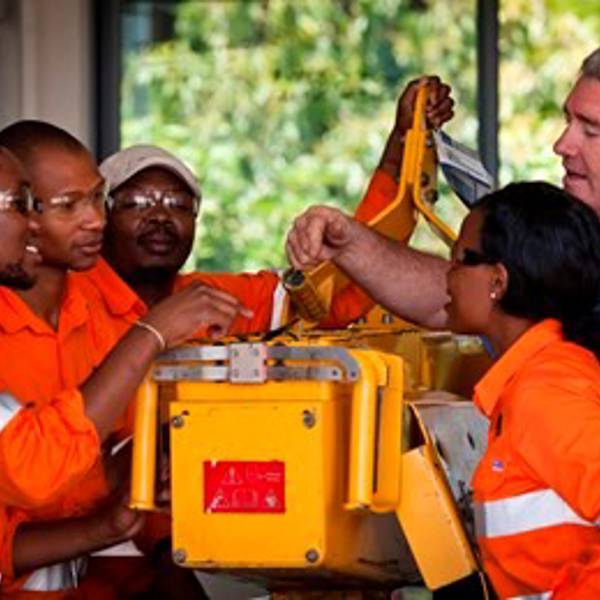
2004
Continued investment in reline crew safety
RME partnered with metallurgist Stephen Kittel to conduct detailed time and motion studies of mill relines globally. These studies pinpointed additional safety and efficiency gaps, inspiring the O-ZONE Liner Lifting Tool range, and precipitating the invention THUNDERBOLT T-MAGs and RUSSELL Elevating Platforms. RME also developed certified training courses with TAFE Queensland to support the upskilling and safety of local reline crews.
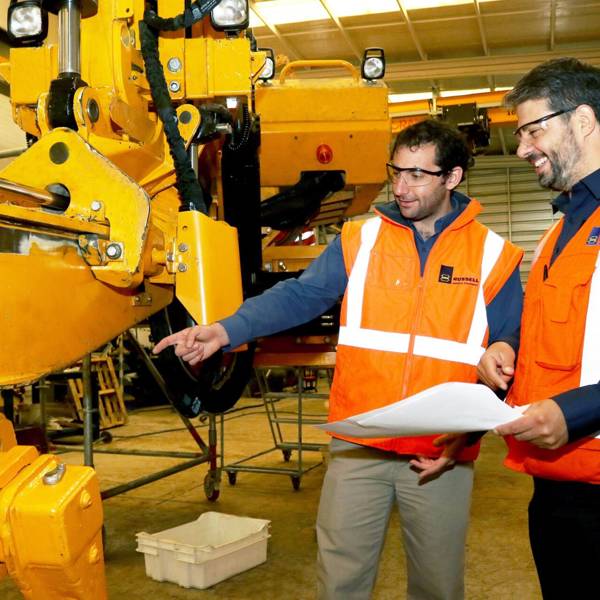
2004
RME South America established
As demand for more advanced, mechanised mill relining solutions grew, RME established its South America operations in 2004 to support a growing customer base in the region. This investment enabled RME to provide specialised expertise and responsive customer support, helping mineral processing operations across South America optimise relining processes, enhance worker safety, and maintain reliable asset support for the RME Mill Relining System. Today, RME equipment operates at over 75 mine sites across nine Latin American countries, and the region hosts RME’s largest cohort of specialised local technical staff outside of Australia.
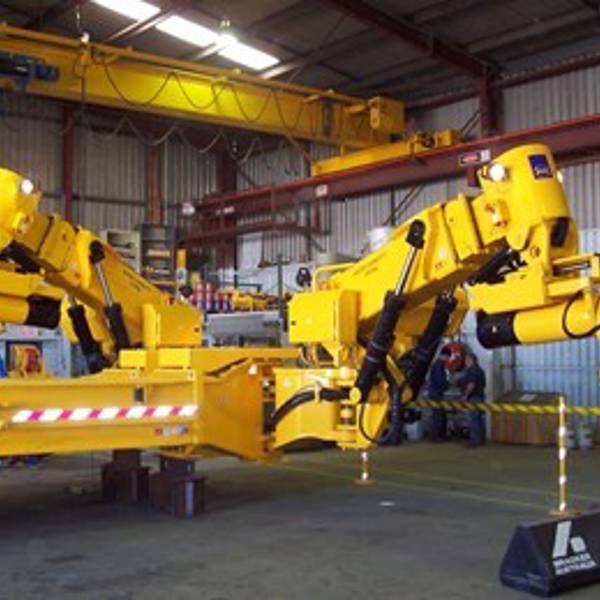
2007
World's first RUSSELL TWIN MRM
RME’s 100th RUSSELL MRM was built for Gibraltar Mine in British Columbia, Canada. It was painted gold to commemorate its place in RME history. In the same year, RME built the world’s first RUSSELL TWIN MRM for BHP Minera Escondida Mine in Chile. RUSSELL TWIN MRMs are two totally independent mill relining machines that can deliver a genuine doubling of mill relining productivity. Over 17 RUSSELL TWIN MRMs are now in use around the world, with 14 of those in South America.
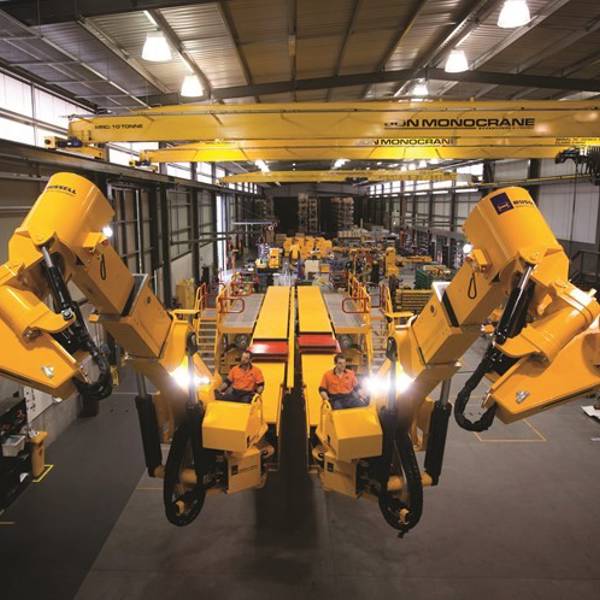
2009
World-class manufacturing facility built
2009 saw the establishment of RME’s operations in North America to support its growing Customer base in the region. In April of that same year, RME moved into its purpose-built, world-class, ISO-certified manufacturing facility at Hursley Road in Toowoomba. The new facility provided the team with the necessary resources to scale up manufacturing and expand workspaces for the engineering teams working on product development.
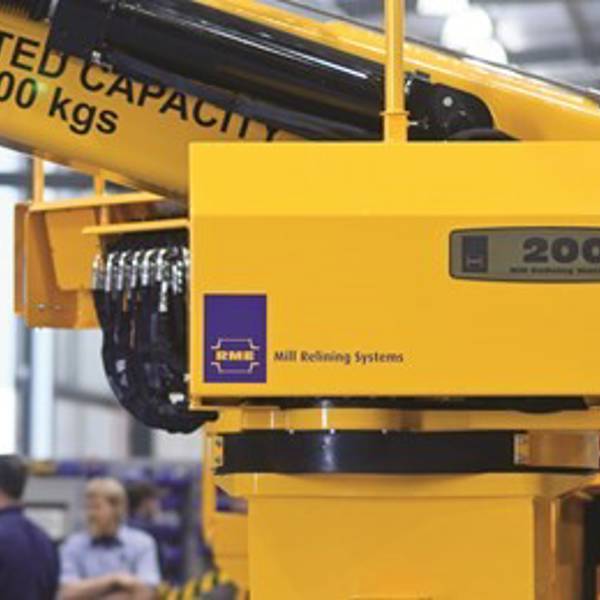
2010
200th RUSSELL MRM
RME built its 200th RUSSELL MRM for BHP Billiton’s Kambaloda Nickel mining operations in Western Australia. MRM #200 was a RUSSELL 7 with a rated capacity of 2500kg for servicing the site’s 26' x 17' SAG mill.

2012
Africa operations and global support and training centre established
In 2021, RME expanded into Africa, including South Africa, to serve this important developing market and its Customers in the region. That same year, RME’s completed and commissioned its global Customer Support and Training Centre at its Hursley Road Headquarters in Toowoomba, Queensland, Australia.
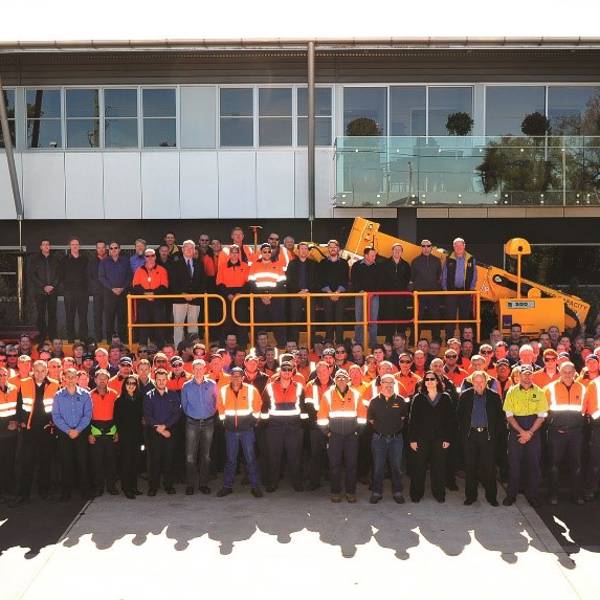
2013
300th RUSSELL MRM
RME celebrated its 300th RUSSELL MRM, built for the Dugald River Mine in North-West Queensland, one of the world's highest-grade known zinc deposits. MRM #300 was a RUSSELL 7 with a 1500kg capacity rating and was cleverly engineered as a ‘combo machine’ to service two mills on this mine site – a 22'x14' SAG mill and a 19'x 29'6" ball mill.
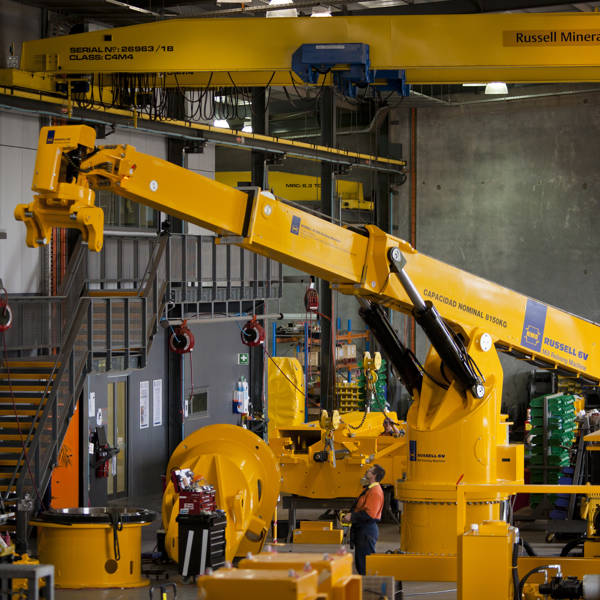
2014
Vertical axis mill relining machines
RME engineered and built the world’s first mill relining machine for vertical-axis stirred grinding mills. The first machine was the RUSSELL 6V Mill Relining Machine developed for the Minera Escondida copper mine in the Atacama Desert, northern Chile.
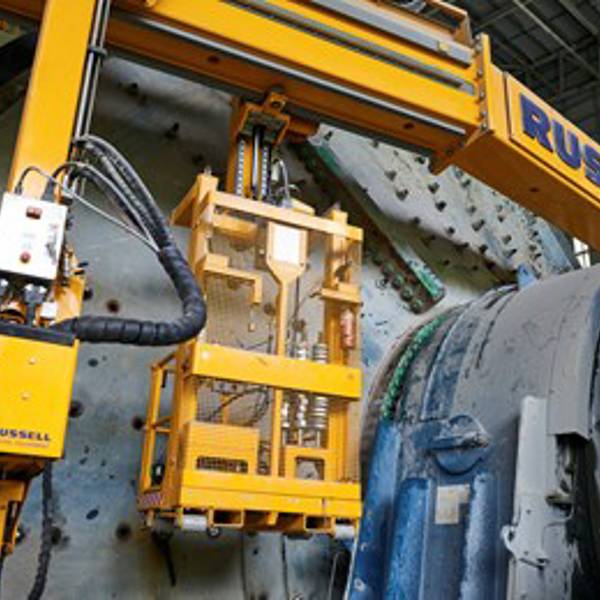
2017
Transforming risk rating and knock-in duration
This year represented a significant expansion of RME’s suite of mill relining safety and performance technologies. RME hosted a demonstrator event to introduce RME INSIDEOUT Technology, RUSSELL SAFETY Products and THUNDERBOLT SKYWAY—RME’s semi-automated suspension and guidance system for roboticising the operation of THUNDERBOLT Recoilless Hammers.
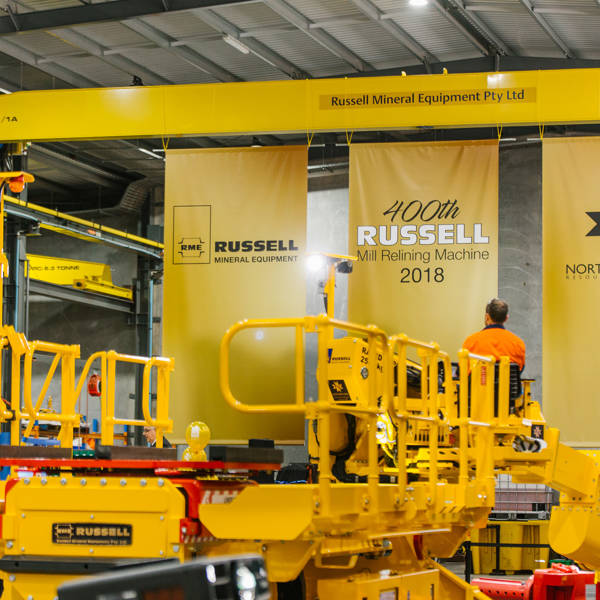
2018
400th RUSSELL MRM
RME celebrated the completion of the 400th RUSSELL MRM, built for Australian gold producer Northern Star Resources Limited. This 400th milestone machine replaced MRM #5, which was originally delivered in 1993. The new model was a RUSSELL 7 2500kg capacity machine for servicing a 24' x 10' SAG mill at the Kanowna Belle mine site near Kalgoorlie in Western Australia.
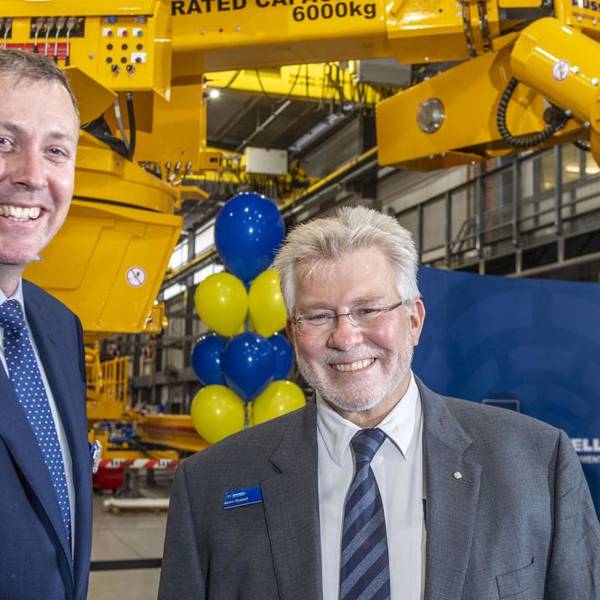
2021
500th RUSSELL MRM milestone
It was under four years after the 400th milestone celebration that RME was commemorating its 500th RUSSELL MRM. This machine was a 7-axis 6000kg capacity for our long-time Customer Northern Star Resources Limited. It was built to service a 36' x 26'60" SAG mill at the company's Thunderbox project in Western Australia. RUSSELL MRM #500 was also delivered with a raft of safety and productivity accessories including a new grapple attachment for safer mucking out, a powered slew linercart, a pivoting floor with integrated seat, and other innovative features designed to enhance safety and efficiency.
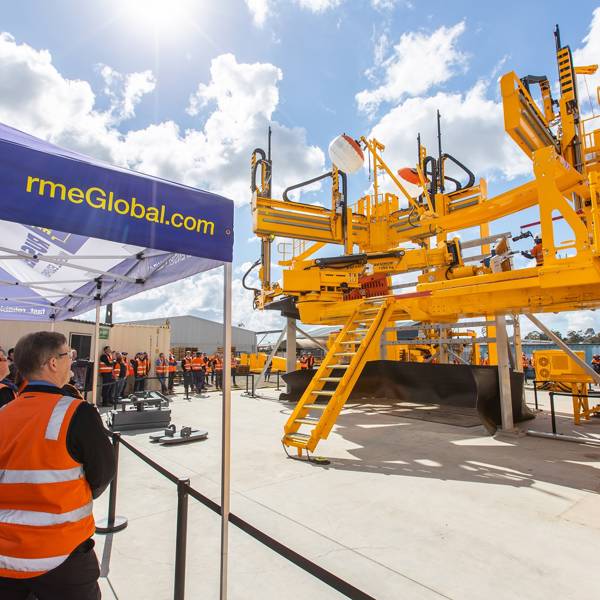
2023
World’s first semi-automated mill relining system!
A major milestone was announced at SAG 2023—the realisation of RME's long-held goal: to provide Customers with remarkable safety and efficiency benefits by enabling relining without anyone inside the hazardous confines of the mill. This vision is now a reality with the RME Advanced Technology Mill Relining System, successfully commissioned at a mine site in Indonesia. The system addresses both worn liner removal and new liner placement phases of mill relining. This success is a result of the extraordinary work by RME's engineering team and strong collaboration with pioneering copper-producing Customers and key industry partners.
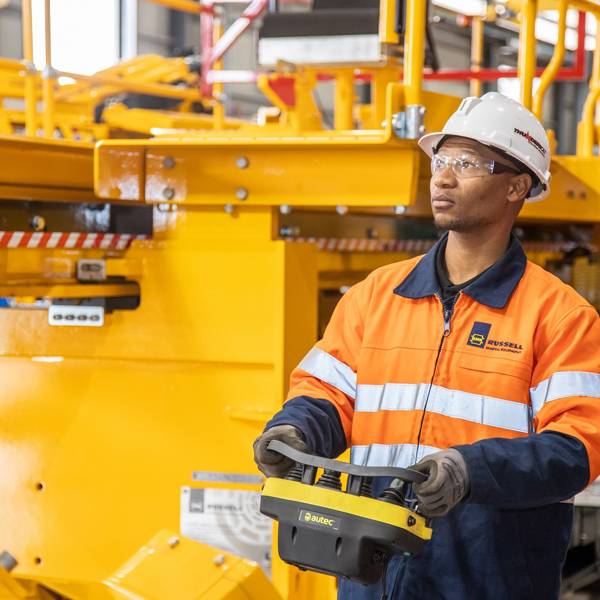
2023
RME expands RUSSELL Liner Exchange Machines
RME announced a significant expansion of its liner exchange machine range, offering accessible options for every mill and mine site. This expansion included additional RUSSELL Mill Relining Machine (MRM) models thanks to its modular, field-upgradeable, AutoMotion-ready platform. Notably, alongside this expansion was the release of the new RUSSELL All-Reach Grapple, which increased the rated capacity of RME's 7-axis machines to 10 tonnes. Value engineering also led to a broader range of cost-effective RUSSELL Mill Liner Handlers (MLHs), ensuring even smaller, cost-constrained mills can improve safety and productivity through high-quality and reliable mill relining solutions.
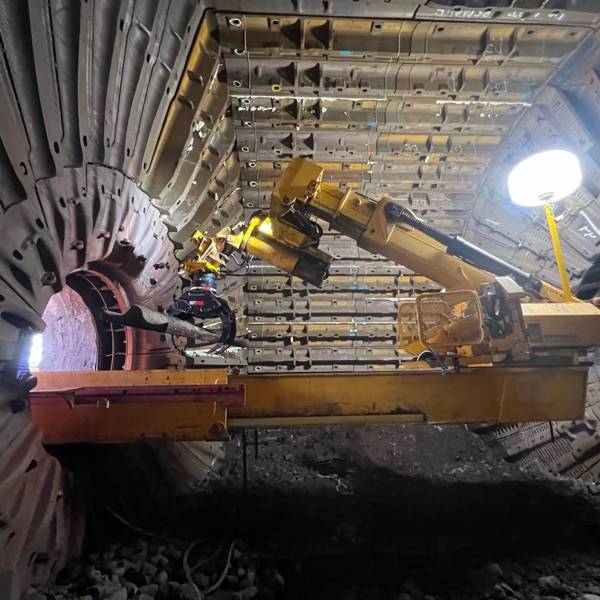
Today
Our mission continues
Our ongoing investment in innovation continues to improve safety for reline crews and increase mill availability. The now mature RME Advanced Technology Mill Relining System—featuring THUNDERBOLT SKYWAY and SKYPORT for automated knock-in, RME INSIDEOUT Technology for safer mucking out and external bolting, along with the RUSSELL 7-R AutoMotion MRM—demonstrates this commitment. These advancements are eliminating the need for crew inside the hazardous confines of the mill, and we're determined to make this technology widely accessible. Even after 40 years, our commitment to optimising the performance potential of every Customer's mill relining system remains stronger than ever. We are RME.
Supporting our Customers
RUSSELL Mill Relining Machines manufactured since 1985
RUSSELL MRMs still in service and supported by RME
THUNDERBOLT Recoilless Hammers manufactured since 1990
Mine sites / Countries with RME equipment
International Sales and Service Centres
Employees worldwide
The RME Team
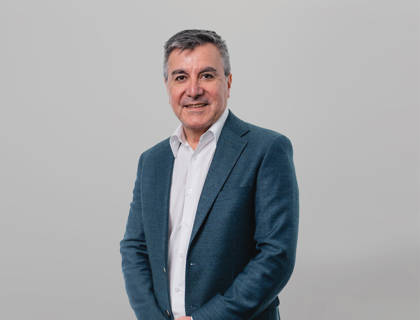
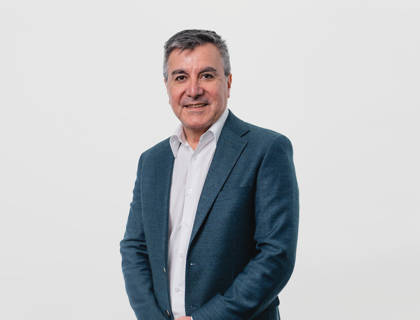
Manuel Galvez
Regional General Manager, South America, Leadership Team
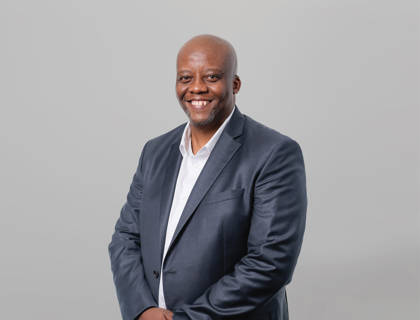
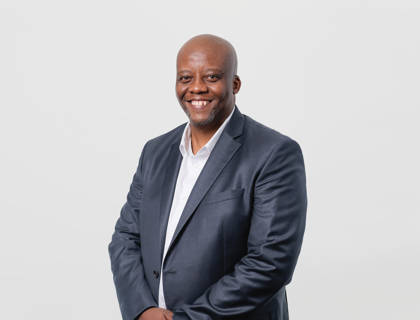
Kabelo Mogobye
Regional General Manager, Africa & South Africa, Leadership Team
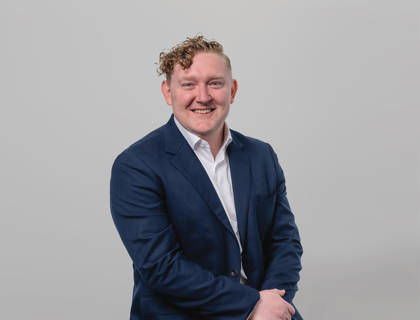
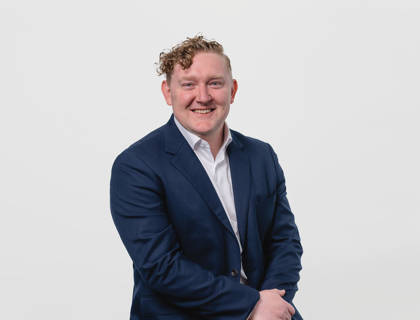
Owen Flemming
Regional General Manager, North/Central America, Leadership Team
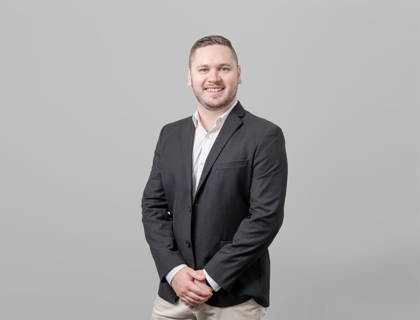
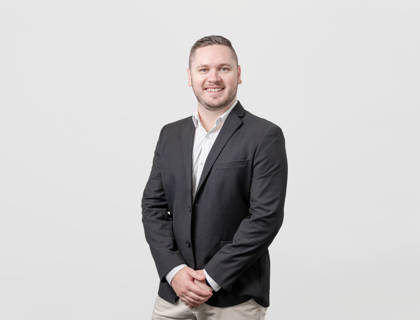
Joshua Bryant
Global Manager, Production Planning
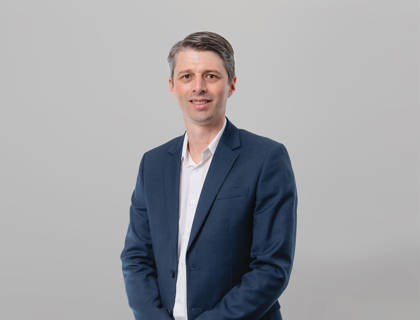
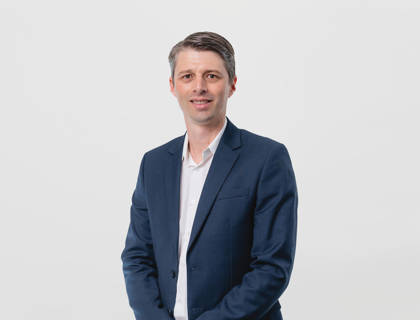
Peter Mann
Global Business Development Manager, Small Mill Solutions
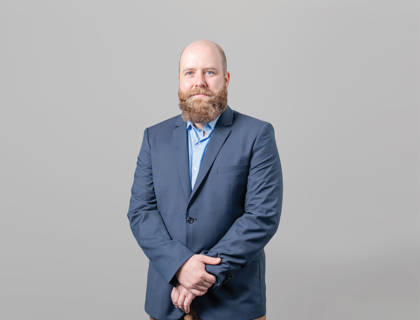
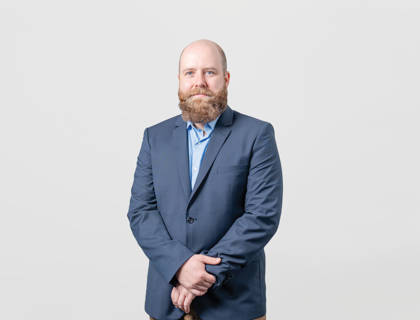
Brent Stevenson
ETO TAKT Manager
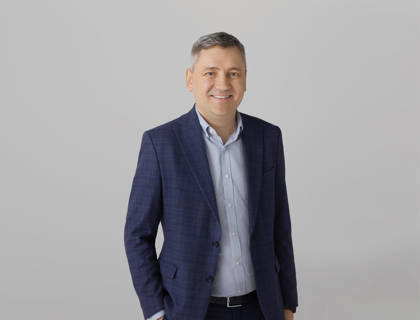
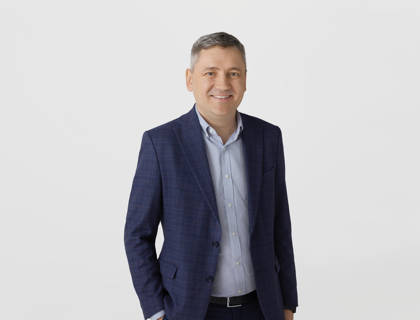
Evgeny Klyukin
Business Development Manager, Central Asia/Middle East/Europe/South Asia
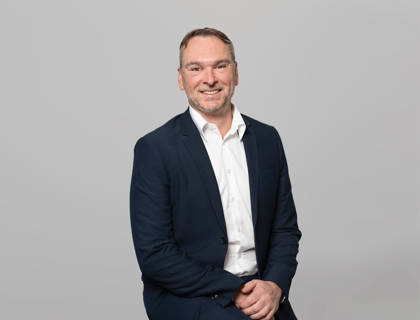
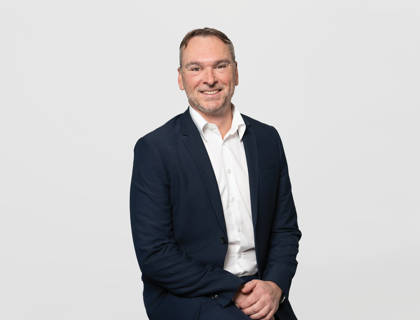
Tim Kruger
Service Account Manager, East Coast & South Australia
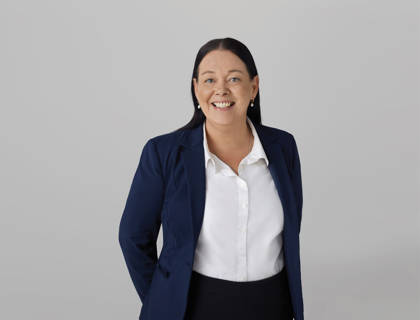
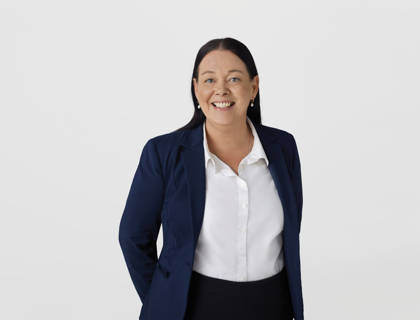
Stacey Parker
Customer Support Specialist, WA
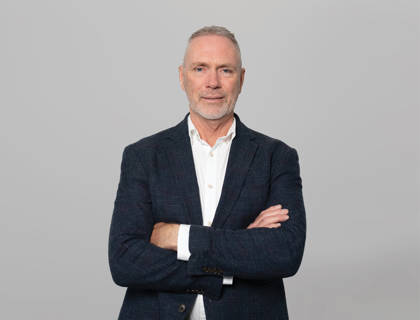
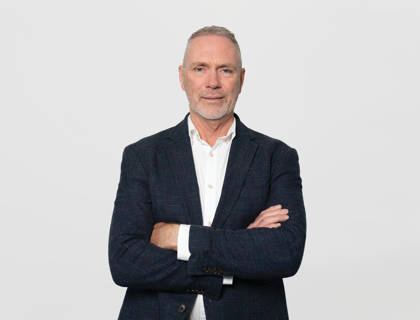
David Green
Customer Support Specialist, APAC
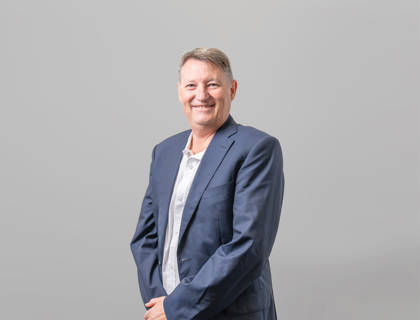
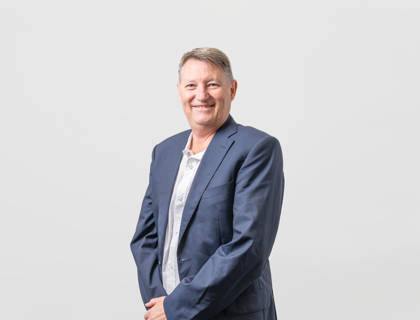
Darren Wall
Customer Support Specialist, APAC
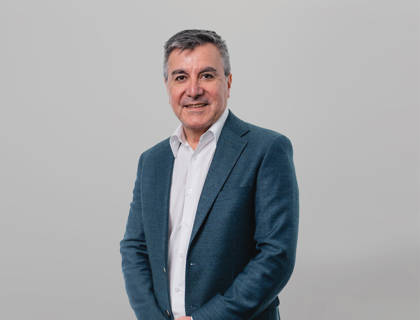
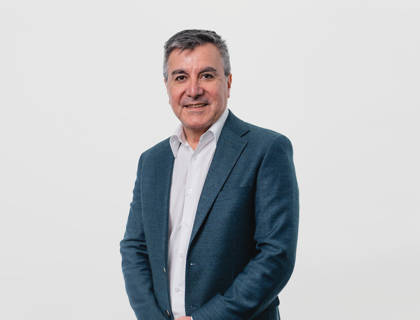
Manuel Galvez
Regional General Manager, South America, Leadership Team
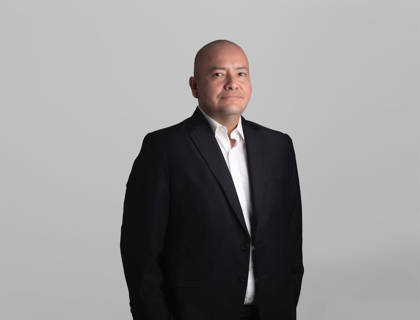
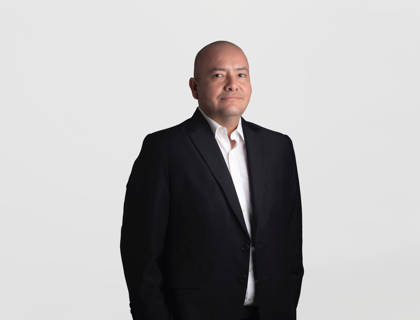
German De La Cruz
Business Development Manager, RME South America
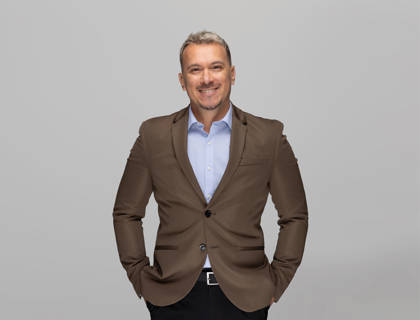
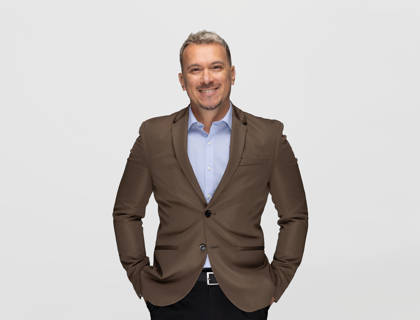
Alexis Valenzuela
Customer Support and Contract Coordinator, South America
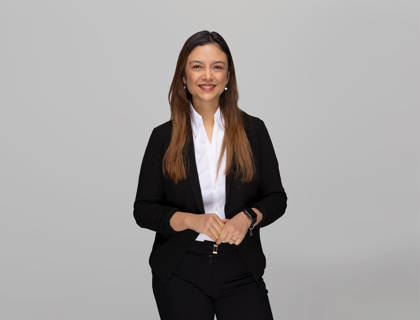
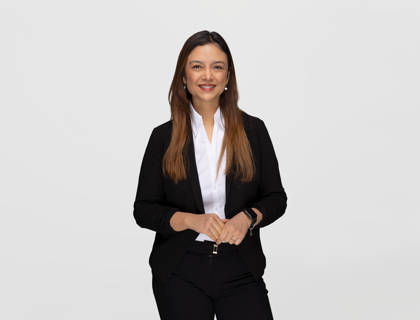
Priscilla Lazcano
Customer Support and Contract Coordinator, South America
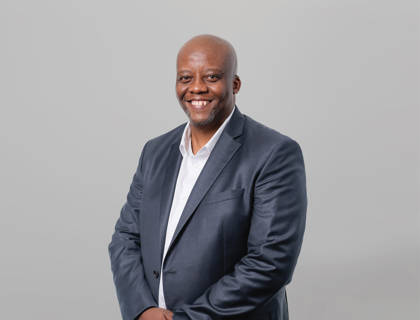
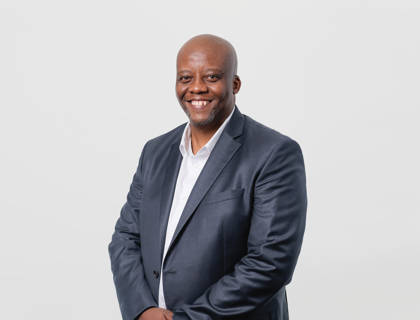
Kabelo Mogobye
Regional General Manager, Africa & South Africa, Leadership Team
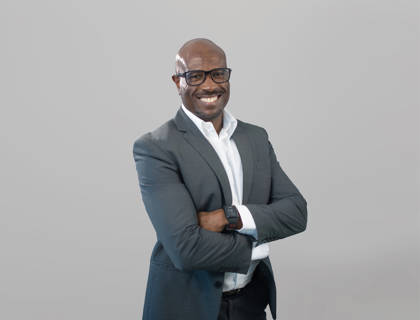
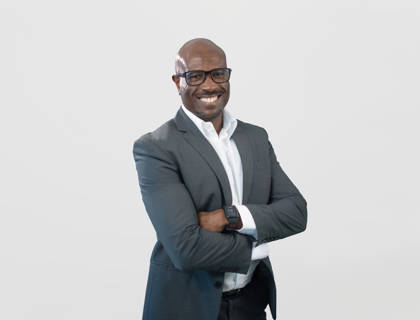
Vusi Mashinini
Operations Supervisor, Africa & South Africa
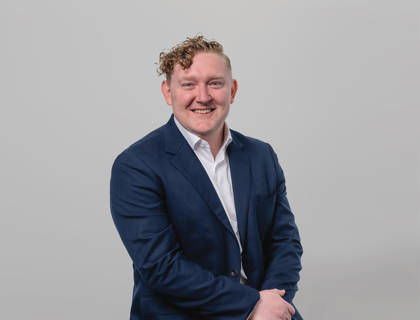
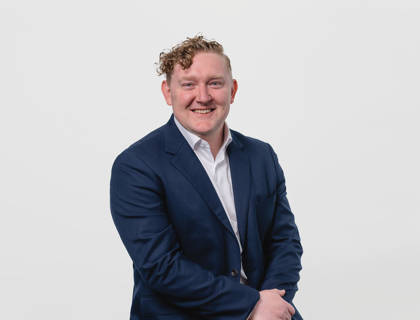
Owen Flemming
Regional General Manager, North/Central America, Leadership Team
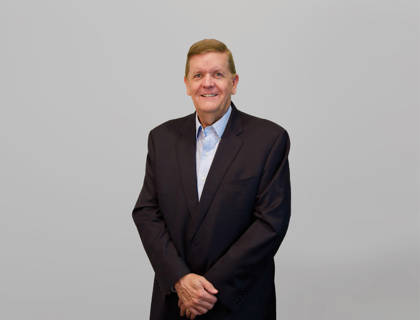
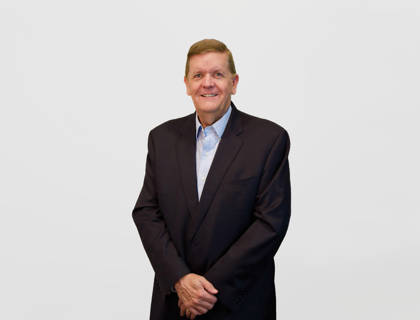
Denny Wisely
Vice President Sales & Business Development, North America
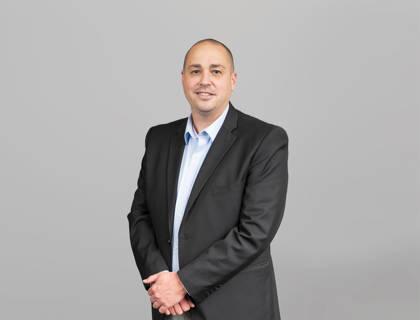
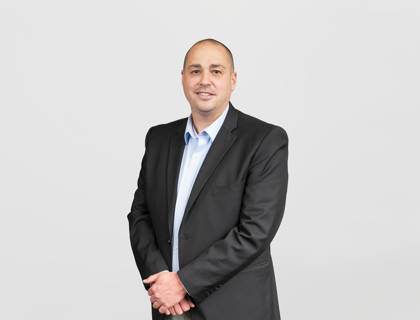
Eric Barber
Operations Manager, North America
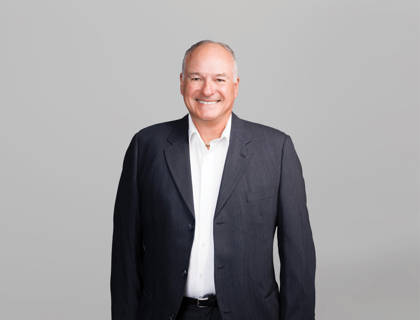
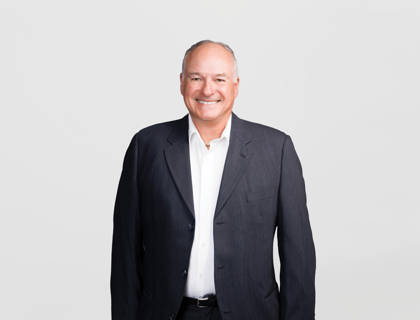
Lyle Hobbs
Service Account Manager, North America
Want to join our team?
RME is a diverse, inclusive team of engineers, manufacturers, and robotics experts who are passionate about providing innovative solutions to the mineral processing industry. If you are interested in a rewarding career in engineering, manufacturing, or robotics, we encourage you to apply.
What we do
Discover our highly efficient and cost-effective mill relining products that has been proven to save our clients millions of dollars in maintenance and downtime expenses. Let us help you achieve significant cost savings and maximize your productivity with our mill relining expertise and commitment to quality.