18 February 2025
To rebuild or replace legacy mill relining equipment—that is the question!
For mill operators, reliable equipment is crucial for short shutdowns and low TCO. With RUSSELL MRMs typically performing well for over 15 years and many still active beyond 20 years, when should you rebuild or replace your aging machine?
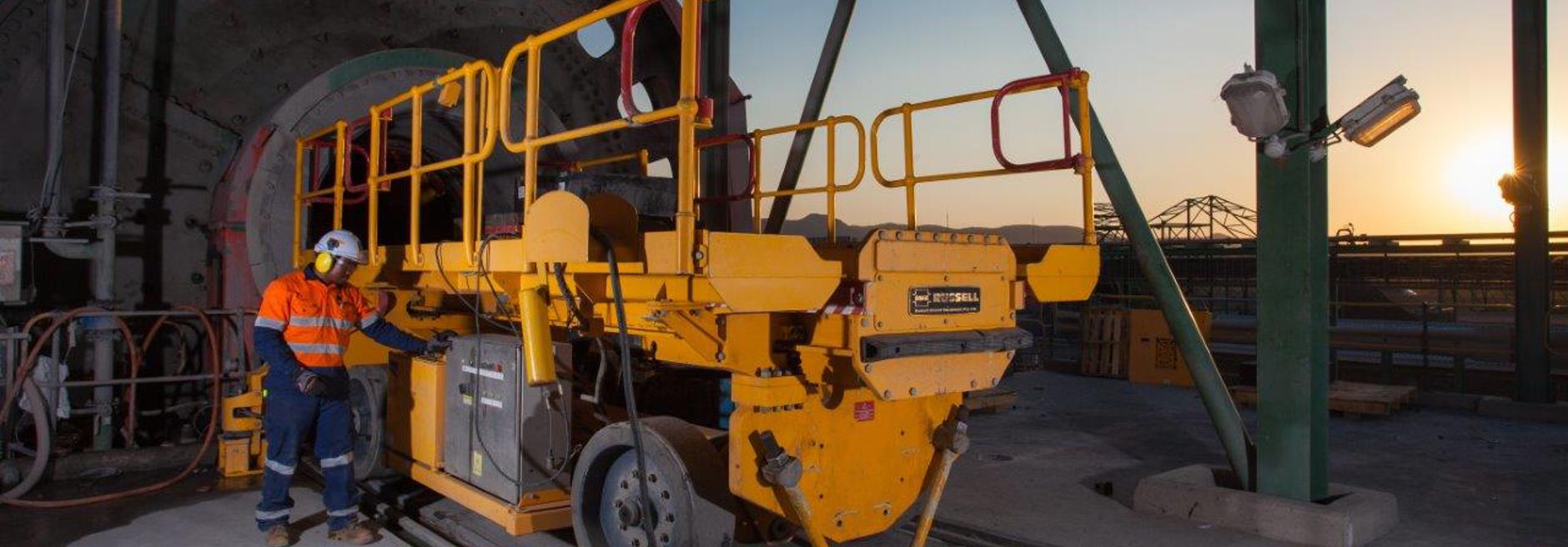
For mill operators, the reliability and longevity of relining equipment play an important role in operational efficiency and in keeping the total cost of ownership (TCO) low. Firstly, reliable, longer-lasting equipment decreases the frequency and cost of repairs, as well as the need for sooner-than-planned capital expenditure replacements. Additionally, this reliability also supports consistent production output by maximising relining productivity and minimising shutdown duration, thereby delivering stronger returns on investment (ROI) and asset usage (ROA).
With a 40-year history of serving the global mineral processing industry, RUSSELL MINERAL EQUIPMENT (RME) often sees its RUSSELL Mill Relining Machines (MRMs) providing reliable service for over 15 years in the field, with many well-maintained assets still active beyond the 20-year mark. This remarkable durability prompts a crucial question among RME Customers: when is it time to rebuild or replace their aging liner exchange machine? While the answer isn’t straightforward, it often becomes clearer when we step through a few considerations.
Signs it might be time to consider the rebuild vs replace question
All mill relining assets—indeed all mining assets—experience wear and tear, but the rate and severity of this deterioration can vary significantly across different sites. This variability can stem from several factors, including differences in care and maintenance, storage practices, and operator handling techniques. For example, has the MRM been used incorrectly or improperly to bash or yank difficult-to-remove liners, instead of using fit-for-purpose attachments, potentially accelerating material fatigue?
Additionally, specific mill relining conditions encountered during the relining process that might have resulted in unintended impact damage or shock loading events, along with the presence of harsh, corrosive environmental elements like temperature extremes, salinity, humidity, UV, dust, and other contaminants, can all contribute to the wear and tear of mill relining assets.
While many sites will have a regular MRM maintenance program in place to address these issues, some lack the required rigor. As a result, more Customers are turning to RME for robust equipment servicing, ensuring optimal reliability and safety throughout the equipment's lifecycle. This attention to maintenance also contributes to longer lifespans for the equipment.
To determine whether it is time to consider the rebuild vs. replacement decision, equipment owners can ask themselves the following questions:
- Is part consumption accelerating?
- Are maintenance costs on the rise, with operators expressing concerns?
- Is reliability becoming an issue, leading to more frequent relining interruptions and extended mill downtime?
- Is outdated or un-upgradeable technology affecting productivity and safety risk and compliance?
If the answer to any of these questions is a yes, it is likely time to investigate your options.
What qualifies as a rebuild candidate?
The decision to rebuild a RUSSELL MRM involves a meticulous examination of various factors, with the life of mine (LOM) often being one of the initial and primary considerations. Sites approaching mine completion may lean towards extending the life of existing assets rather than replacing them. Whereas those sites with a longer operational life may seek to leverage the advancements in productivity, serviceability, safety, and cutting-edge automation technology offered by new machines.
"The maintenance history of the equipment is equally vital. Was the asset serviced at proper intervals? Is the asset fundamentally sound, despite showing signs of wear and tear? Is the current condition of the asset economically viable for restoration to meet the required safety and performance standards in its second life? Additionally, assessing whether a site can afford the downtime associated with a rebuild—particularly if the machine is the sole asset servicing a high-throughput mill—is also an important consideration."
Expert guidance from leading suppliers
Leading original equipment manufacturers (OEMs) with a long history of supply, like RME, possess extensive data-driven knowledge regarding the costs, risks, and benefits integral to the decision-making process of rebuilding or replacing mill relining machines. Through analysis of site-specific needs and asset condition, we provide defensible insights into maintaining the productivity and safety of aging equipment or guidance for Customers opting for a timely end-of-life (EOL) transition to a newer, higher-performing mill relining system.
The rebuild major service process
A RME Rebuild Major Service stands out as the most comprehensive form of RUSSELL Mill Relining Machine servicing. The primary objective is to restore all systems, subsystems, and components to either new or near-new condition and performance. Beyond the sustainability benefits associated with reduced raw material consumption and energy inputs associated with the production of new machines, rebuilds offer an opportunity to upgrade productivity and safety technologies to align with evolved mine site objectives.
Did you know?
The RME Rebuild Major Service for RUSSELL Mill Relining Machines includes approximately 400 tests and inspections, and reconditioning or replacement of around 4500 parts.
Executing a rebuild major service is a significant undertaking, requiring specialised skill sets, tooling, and processes. Mine sites must ensure that MRM rebuilds adhere to the highest standards, re-undergo comprehensive load capacity testing, and receive certification from the OEM. RME goes a step further to augment the value of certified rebuilds by providing exclusive as-new warranties, updated documentation, and continuity of digital histories across the first and second life of the RUSSELL MRM. This aids in fostering improved and more informed decision-making, particularly crucial for considerations related to safety, risk, and compliance.
A recent case study
RME recently assisted a mine site in the Asia Pacific region with the challenge of deciding whether to rebuild or replace their 20-plus-year-old RUSSELL Mill Relining Machine. Collaborating closely with the site, we evaluated the rebuild vs. replace scenario. Considering the planned long mine life, the site determined that a new machine was the optimal solution, ensuring another 20+ years of fast, reliable, and safe service.
"Additionally, the productivity features and serviceability improvements of our machines have significantly advanced since the delivery of the Customer's first MRM. Prioritising the latest safety technology, the new machine was equipped with the RUSSELL Safe Beam Traverse, RUSSELL MILLBRITE In-Mill Lighting, and the RUSSELL Liner Lever."
We are ready to assist you
With almost 40 years of experience in the global mill relining industry, RME possesses unparalleled depth and breadth of knowledge in this field. Our expertise ensures we can support your operation in making the right decision—whether it’s rebuilding or replacing your equipment. We also offer insider knowledge and practical methods to maximise equipment reliability and lifespan, keeping your total cost of ownership (TCO) low, while boosting your returns on investment (ROI) and asset usage (ROA) high through increased mill availability. Reach out to our application experts via your nearest international sales and service centre. We look forward to supporting you.
Content related to this article
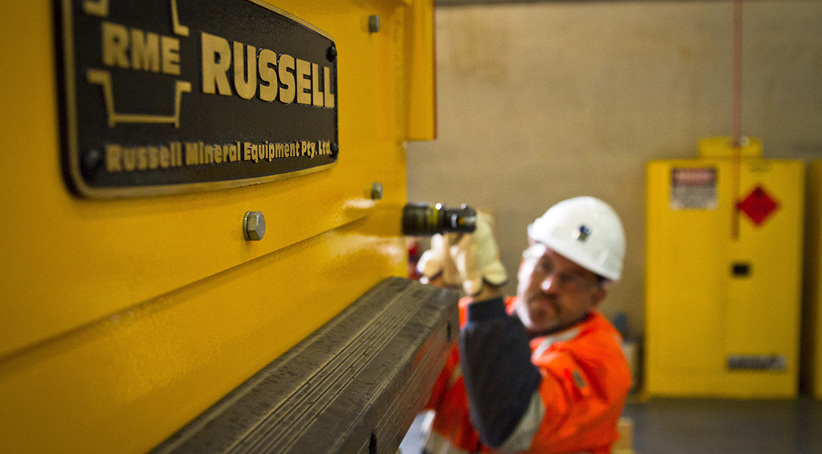
RME REBUILD MAJOR SERVICE
Restore the performance of your original machine and benefit from a new warranty and the latest engineering and safety updates. Give your MRM a second life.
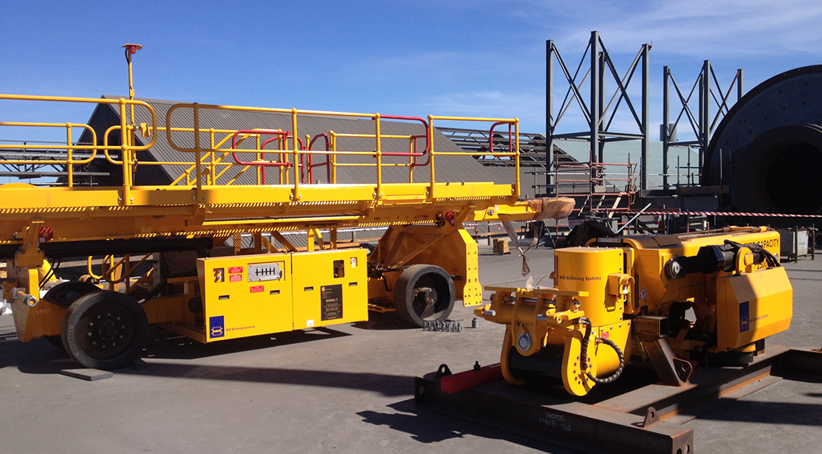
LIFE EXTENSION MAJOR SERVICE
An RME Life Extension Major Service ensures that all equipment components, are inspected, tested, refurbished and replaced, where required.
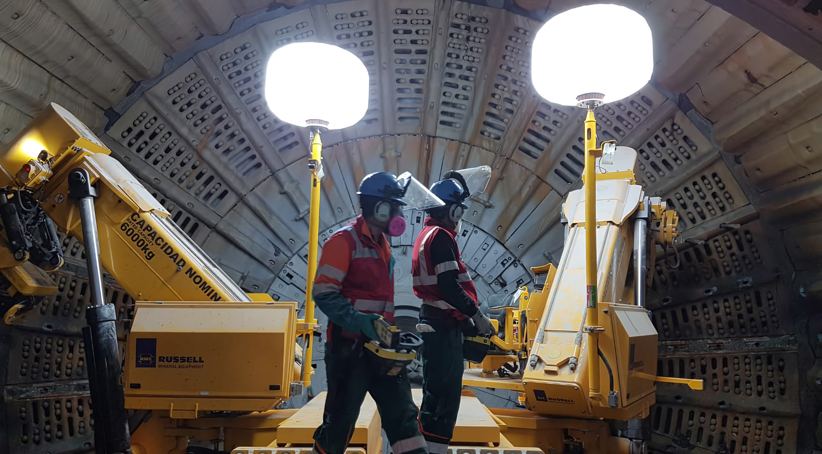
RUSSELL LINER EXCHANGE MACHINES
The trusted choice for mill operators globally. Our expanded, higher-performing range – from <400 kg to 10 tonne capacities – ensures fast, reliable, safe mill relining is available to every mine site.
Read More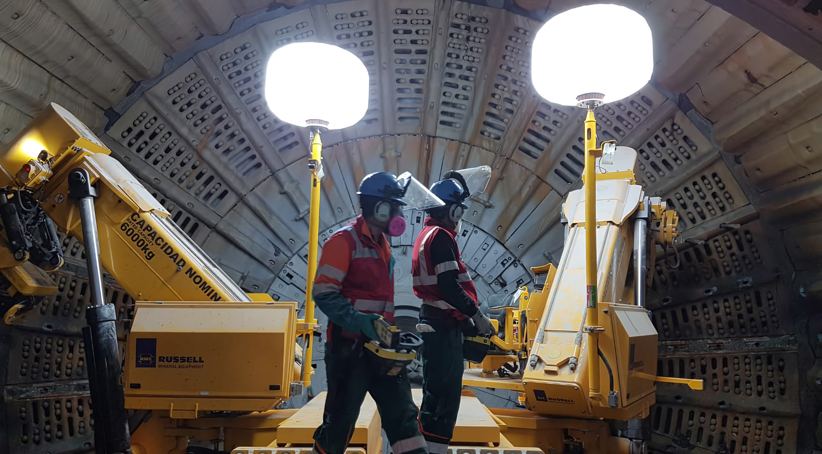
WE ARE HERE TO HELP
We ensure Customers have access to trusted OEM engineering know-how where and when they need it. Here's how to contact RME.