26 August 2024
RME wins QMIHSC 2024 Safety Innovation Award
RUSSELL MINERAL EQUIPMENT (RME), has taken out the 2024 Queensland Mining Industry Health and Safety Conference (QMIHSC) Innovation Award for it's 'RME Advanced Technology Mill Relining System'.
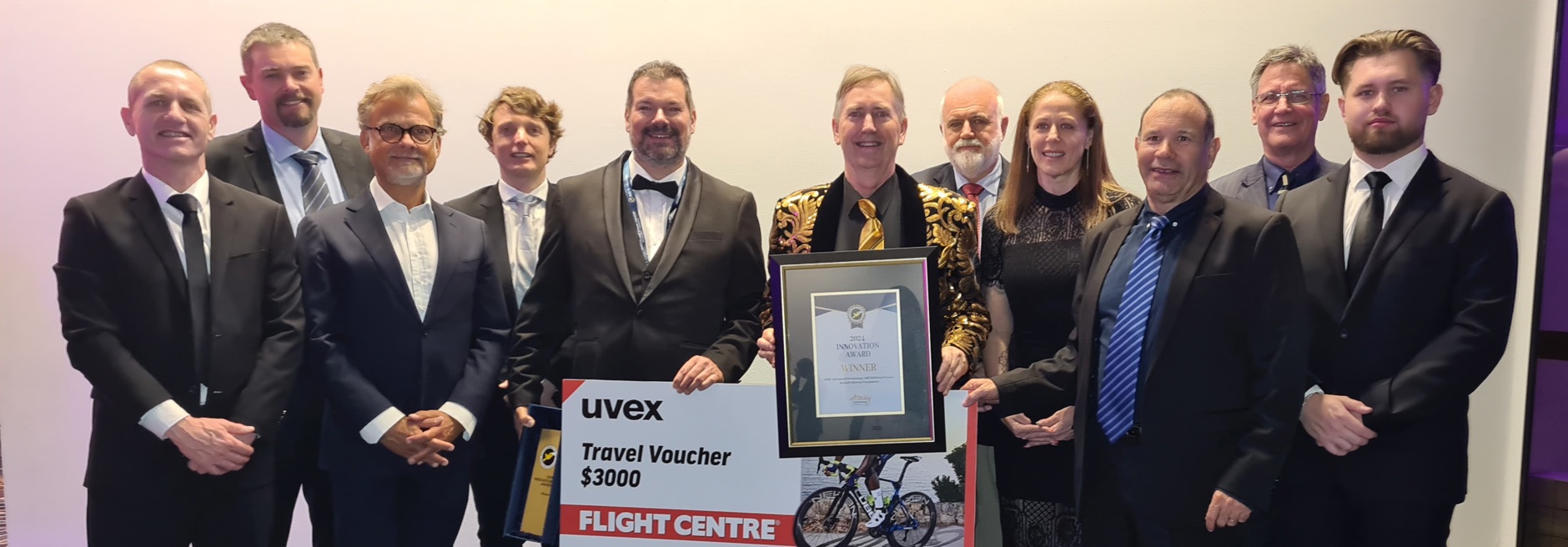
Mill relining systems Original Equipment Manufacturer (OEM), RUSSELL MINERAL EQUIPMENT (RME), has won the 2024 Queensland Mining Industry Health and Safety Conference (QMIHSC) Innovation Award.
The Award recognises RME's Advanced Technology Mill Relining System for its use of automation to eliminate the need for crew to enter the mill during liner exchange, delivering significant safety and commercial outcomes for Customers and the wider industry.
Furthermore, as RME approaches its 40th anniversary, the Award recognises RME for once again raising safety standards in the mill relining industry, demonstrating its unwavering commitment to safety leadership.
RME Founder, Executive Chairman and Chief Engineer, Dr John Russell celebrated the recognition of RME’s inventive engineers and wider team, along with the contributions from Customers and suppliers.
“We extend our sincere gratitude to the judging panel for recognising the significance of this extraordinary achievement by our engineers, project collaborators, industry partners, and Customers. This innovation marks a new era of safety for reline crews.”
“We applaud the many worthy nominees, finalists and the winners of the highly commended and people's choice awards. We thank the conference organisers and uvex for sponsoring the award.”
This year the conference theme was 'Back to the Future', with QMIHSC posing the question, “Can simpler processes coexist with new technology and work methods?” Using real-world examples, RME proudly demonstrated to the judging panel that indeed, it can.
While mill relining is a significantly safer process since the invention of the RME Mill Relining Machine nearly 40 years ago, RME understood from its work with reline crews that some risks remained in certain parts of the process.
With creative problem-solving being core to RME’s cultural DNA, RME’s team worked closely with mill operators and reline crews to identify where these remaining hazardous and manually repetitive tasks could be eliminated or substituted.
RME then worked to ‘engineer the risk out of mill relining’ by roboticising existing, proven and confidently-used relining systems, engineering faster and safer methods that reduce risks for reline crews and improve mill availability.
Additionally, RME’s modular platform and staged implementation program ensure these methods are readily accessible to grinding mills large, medium and small.
“The question posed by QMIHSC is one we have constantly asked of mill operators, reline crews, industry technology partners and ourselves over the past 40 years, as we strive to enable our Customers to remove fatal risk through innovative solutions,” Dr Russell added.
“At RME, people-centred innovation is a constant. It’s our DNA, our way of being, our promise to our industry and our ongoing purpose – for the hundreds of reline crews we support today and the hundreds to come in the future.
“We are thrilled that our dedication to safety – combining the reliability of the past with the cutting-edge technologies needed for the future – is gaining recognition."
An automated system that is greater than the sum of its parts
RME's Advanced Technology Mill Relining System addresses the two main phases of mill relining: worn liner removal and new liner placement and enables the completion of these necessary maintenance processes without anyone inside the mill. This Advanced System was developed and implemented in concert with some of RME’s existing Customers, including strong collaboration and change management with site management and reline crews.
The centrepiece of RME’s semi-automated mill relining system – the RUSSELL 7 Model R AutoMotion™ Mill Relining Machine (MRM) – adds robotics capabilities to the industry’s most adopted 7-axis liner exchange machine, the RUSSELL 7 MRM.
It is complemented by THUNDERBOLT® SKYWAY, which roboticises the operation of THUNDERBOLT® Recoilless Hammers, used for ‘knock-in’ on the exterior of the mill. Operational since 2020 at sites in Central America and Indonesia, SKYWAY is well-proven. This technology is now also available as a portable lift-in solution called THUNDERBOLT® SKYPORT.
These systems, working together with RME INSIDEOUT™ Technology tooling and compatible liner and bolt design, can grab knocked-in worn liners off the shell or from the charge and place new liners against the shell with millimetre precision and without personnel working inside the mill. The securing of liners, nuts and bolts from the mill’s exterior can also now be achieved using RME BOLTBOSS™.
Over 30 mill relines globally have now used products from RME’s Advanced Technology suite, demonstrating its broad applicability. Filmed studies of these relines demonstrate these methodologies are both safer and faster for mill operators and reline crews.
About RUSSELL MINERAL EQUIPMENT
RUSSELL MINERAL EQUIPMENT (RME) is the world’s leading Mill Relining Systems Technology OEM. We invent machine systems and service-based solutions for problems encountered in the world’s mining and mineral processing industries. Our technologies deliver short shutdowns, high mill availability and safe working environments. Established in 1985, RME has grown to operate in 64 countries, has 13 international Sales and Service Centres and employs more than 450 people worldwide. For more information about RME: www.rmeglobal.com
Media contact
Emma Needham
+61 (0)400 266 659
emma@emmaneedham.com.au
High resolution images are available upon request.
Content related to this article

WE ARE RME
RME is the world's most trusted original equipment manufacturer (OEM) of mill relining technologies. Our mission is to reduce hazardous risk and improve the availability of mineral concentrators.
Read More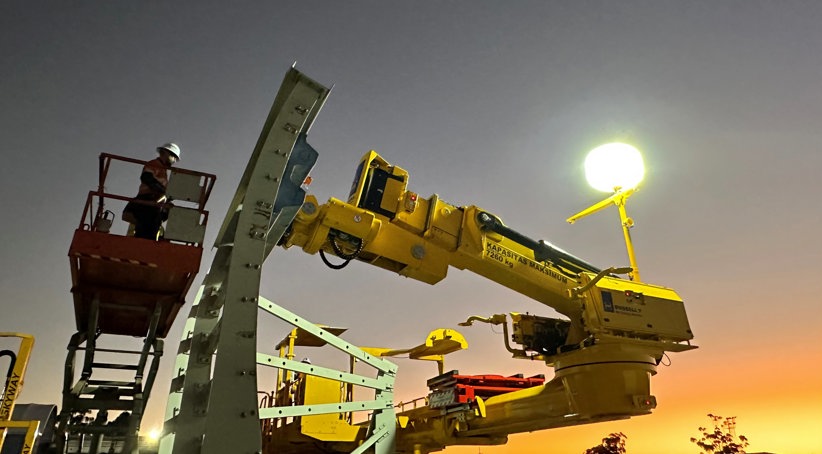
RME ADVANCED TECHNOLOGY
Our relentless pursuit to improve safety and productivity has driven us to engineer a future where relining is performed safely from outside the mill – at faster speeds than ever before.
Read More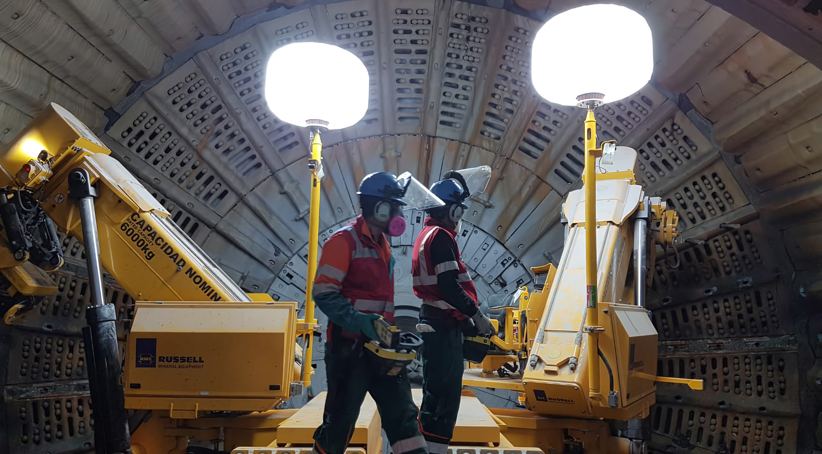
RUSSELL LINER EXCHANGE MACHINES
The trusted choice for mill operators globally. Our expanded, higher-performing range – from <400 kg to 10 tonne capacities – ensures fast, reliable, safe mill relining is available to every mine site.
Read More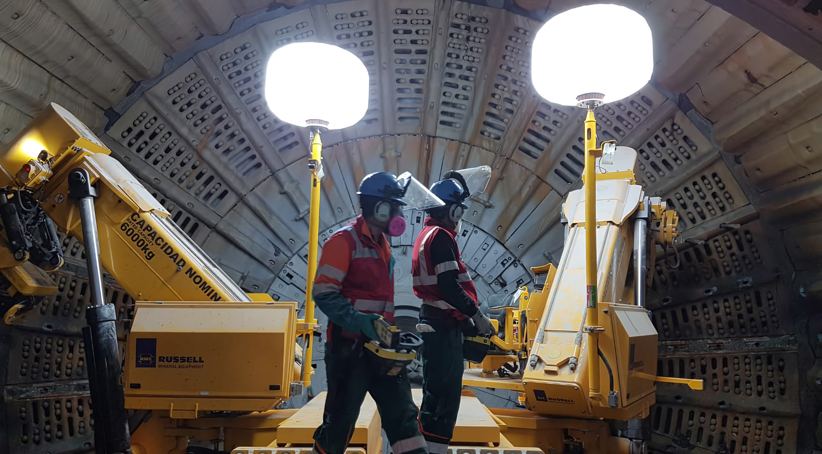
TRUST RME TO RAISE THE STANDARD
Trusted globally for every 40 ft SAG, we're now bringing RME safety, innovation, performance, reliability and long-life standards to even the smallest capacity machines.
Read More