30 November 2023
RME expands RUSSELL Liner Exchange Machine range
RME has announced an expanded range of RUSSELL Liner Exchange Machines to make safer, more efficient and future-proofed relining accessible for every mill and mine.
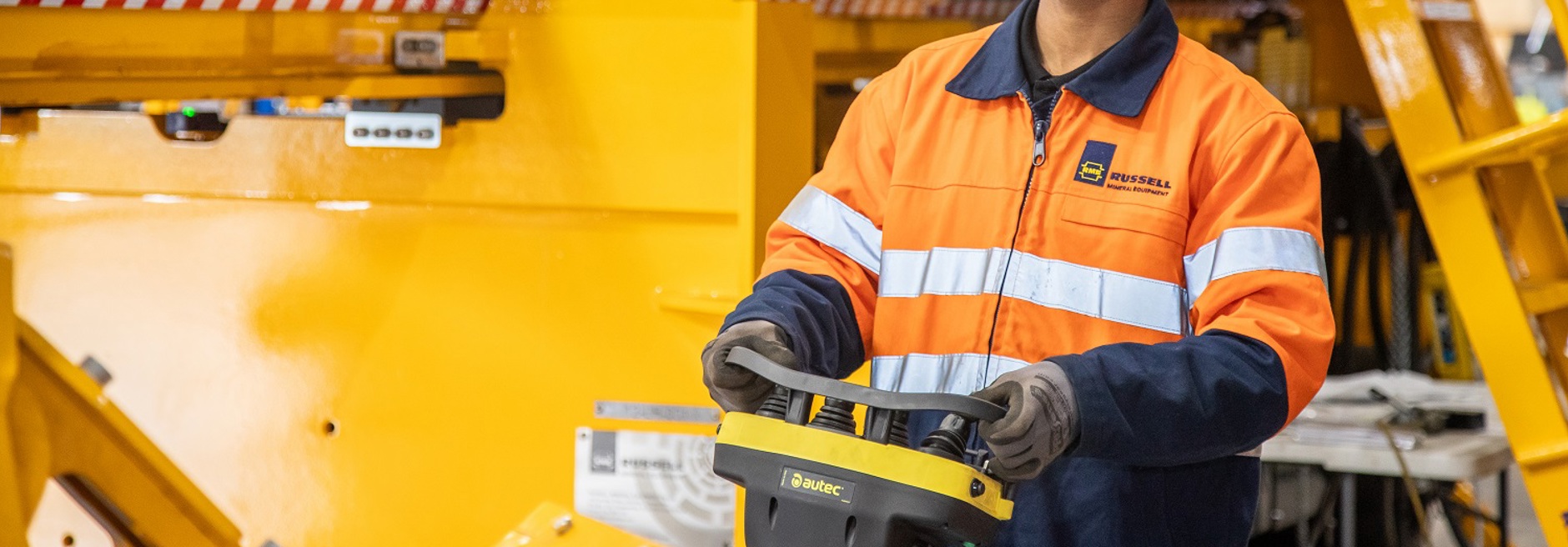
Mill relining systems Original Equipment Manufacturer (OEM), RUSSELL MINERAL EQUIPMENT (RME), has today announced an expanded liner exchange machine range with accessible, future-proofed options for every mill and mine site, from the largest to the smallest.
The expanded range introduces additional RUSSELL Mill Relining Machine (MRM) models with an increase in rated capacity for medium to large grinding mills, made possible by its modular, upgradeable, and AutoMotion™-ready platform.
Value-engineering has also given Customers a wider choice of RUSSELL Mill Liner Handlers (MLHs), ensuring more cost-constrained smaller mills can improve safety and productivity through superior quality and reliable mill relining solutions.
RME Founder, Executive Chairman and Chief Engineer, Dr John Russell described the new range as the embodiment of everything RME has learnt from manufacturing more than 550 RUSSELL Mill Relining Machines (MRMs) for over 35 years.
“Mill relining is one of the most hazardous activities in mineral processing, and put simply, is the reason RME exists – to remove fatal risk through innovative solutions.
“So, if we are to deliver on our company purpose, then it stands to reason that we should work to solve the issue of safe and efficient relining of all mill sizes. There really is no such thing as a lightweight liner.
“Every mill, whether its liners weigh 180 or 9,000 kilograms, needs access to an efficient, reliable, and most importantly, an inherently safe mill relining solution.
““Leveraging all we have learnt over the past 35 years, we have dedicated ourselves to the task of creating the industry’s highest quality mill relining solutions. Now, we offer an even more comprehensive range of technologies, from advanced automation to compact mechanised solutions.”
“I’m proud of the work our team has undertaken to open up our liner exchange solutions platform to ensure every mill and mine site can access safe, fast and reliable mill relining.”
RUSSELL Liner Exchange Machines for every mill and mine site
RUSSELL MRM range
The RUSSELL MRM family now offers Customers an expanded range of models and an increase in rated capacity to 9,000 kg, establishing a new industry benchmark. Top of the range is the RUSSELL 7 Model R AutoMotion™ MRM, recently announced as the world’s first roboticised MRM capable of relining from outside the mill. The RUSSELL 7 Model U MRM is reserved for unique, custom-engineered 7 or 8-axis solutions for highly-specialised grinding mill applications. The RUSSELL 7 Model S+ is future-proofed with RME AutoMotion™-ready hardware for an easy software-only upgrade path to advanced relining. The RUSSELL 7 Model S, serving as the base model, continues as RME’s signature machine for performance and the industry’s most widely adopted MRM. Both the Model S and S+ are upgradeable in-the-field to the RUSSELL 7 Model R AutoMotion™ MRM feature-set. This upgradable platform offers mill operators many advantages, such as greater budget flexibility, more deployment options, increased value and return on technology investment, and ensures mill relining operations can be automated in the future. RME will also continue to offer RUSSELL TWIN 7 MRMs, which enable both sides of the mill to be relined simultaneously, safely increasing reline speeds.
RUSSELL MLH range
The RUSSELL MLH offering for small to medium mills now includes the Model E, Model L and Model LL. The RUSSELL 3/7 Model E 1500 MLH/MRM can be economically purchased as a RUSSELL 3-axis liner handler with future upgradability to 7-axis MRM functionality. The field-proven RUSSELL 3 Model L 1000 MLH gives smaller mills the certainty of industry-best quality and reliability with the means to improve mill availability and safety. Model LL is the MILLMAST POWERSHIFT, an innovative compact carry-in liner handler for small mills with liners up to 400 kg. RME’s smaller capacity mill liner handlers are configured-to-order, reducing end-user cost and delivery lead times, and enabling Customers to realise safety and productivity gains sooner.
RUSSELL V range
RME is also actively promoting its RUSSELL V range, developed for manoeuvring auger liners in vertical axis stirred grinding mills. These mills are gaining popularity due to their reduced energy consumption and increased energy efficiency. In this range RME has the RUSSELL 3V MLH with a capacity of 13T and the RUSSELL 6V MRM with a capacity of 10T.
Eliminating risk through innovative solutions
Along with the newly-expanded liner exchange machine range, RME has also released the new RUSSELL All-Reach Grapple™. This innovative grapple offers a superior centre of gravity and increases the maximum lifting capacity of RUSSELL MRMs to 9,000 kg, the highest in the industry. It also delivers extreme in-mill reach and precision control of liner orientation. The All-Reach Grapple is a standard inclusion on the RUSSELL 7 Model S+ and Model R from 2024 onwards, and is optional for the Model S. All-Reach Grapple retrofits are available for most RUSSELL 7 and 8-axis MRMs in the field.
The RUSSELL Claw is a new grapple attachment from RME’s INSIDEOUT™ Technology suite. It enables MRM operators to retrieve worn liners without the need for crew to work on the charge, or even inside the mill. It can eliminate the manual slinging of worn liners, which until this invention, remained one of the most hazardous tasks in worn liner removal. The RUSSELL Claw is compatible with both 2-pin and 4-pin grapples. All grapples manufactured from 2024 onward are Claw-ready, and RUSSELL 7 and 8 units predating 2023 can be retrofitted for this attachment.
An easy entry to advanced relining
Dr Russell continued, “We’re making it easier than ever to enter the world of advanced relining and achieve visible, defensible and sustainable improvements in concentrator performance and mill relining safety.
“While RME has historically delivered quality solutions to the mid and large-sized mills market segment, we are ideally placed to address the challenges faced by all mills and mine sizes today, and in the future."
Accelerating the journey toward safer and more responsible mining
RME aspires to improve the human condition through responsible access to metals at lower cost. This aspiration carries three responsibilities: to ensure the safety and wellbeing of RME’s people and Customers; to minimise RME’s environmental impact; and to enhance RME’s Customers' mill availability to meet the growing demand for the minerals necessary for decarbonisation.
Dr Russell concluded, “RME believes that future development must balance social, economic and environmental sustainability for the ongoing improvement of the human condition. That same belief underpins our inventions.
“Through collaboration with our suppliers and Customers, we have made mill relining safer and faster, while also positively impacting local jobs, livelihoods and living standards in the regions where we operate.
““RME’s liner exchange machines are also electro-hydraulically powered, and unlike fossil fuel-driven mining equipment, are ready for sustainable energy sources without requiring power system modifications.”
“We are delighted to be able to play a part in safely and responsibly enabling the efficient production of the metals and minerals that are essential to decarbonising our economies.”
About RUSSELL MINERAL EQUIPMENT
RUSSELL MINERAL EQUIPMENT (RME) is the world’s leading Mill Relining Systems Technology supplier. We invent machine systems and service-based solutions for problems encountered in the world’s mining and mineral processing industries. Our technologies deliver short shutdowns, high mill availability and safe working environments. Established in 1985, RME has grown to operate in 64 countries, has 12 international Sales and Service Centres and employs more than 450 people worldwide.
For more information about RME: www.rmeglobal.com
For more information about RME’s expanded liner exchange machine range: https://www.rmeglobal.com/what-we-do/mill-relining-equipment/liner-exchange-machines/