06 August 2024
Training matters when it comes to mill relining safety
Inadequate training and supervision has been shown to escalate risks in mining. The same is true for mill relining. RME's 40 years in the industry has taught us the importance of this issue for safety. Today’s blog shares our learnings.
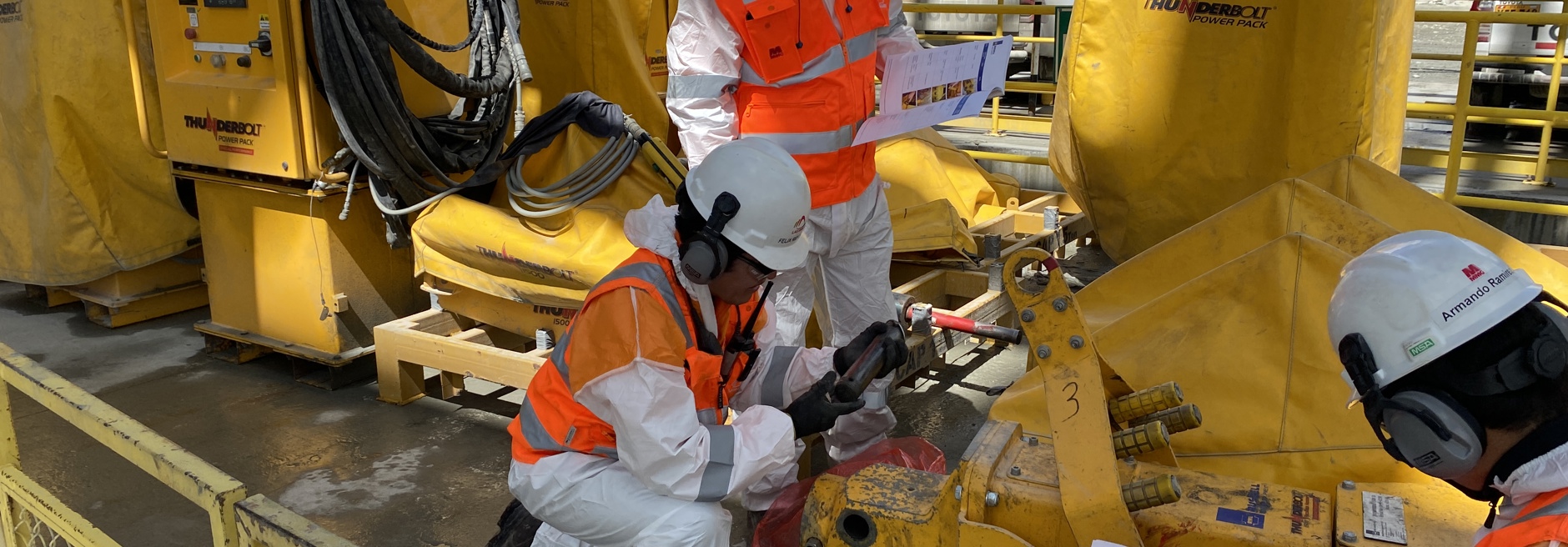
Mill relining safety has improved since RUSSELL MINERAL EQUIPMENT (RME) introduced mechanised mill relining in 1985. While incident rates have trended steeply downwards, this necessary task remains one of mining’s most hazardous maintenance activities. Incidents, when they occur, can risk serious consequences: equipment damage, unplanned downtime, costly shutdown delays and, worst of all, devastating injuries, and fatalities.
The role of training in reducing fatal risk
The 2020 Brady Review into fatal accidents in Queensland (Australia) mines and quarries from 2000 to 2019 highlighted a sobering reality: more than 50 per cent of these accidents involved either inadequate or non-existent task-specific training and competencies. An even greater portion of these accidents involved absent or insufficient supervision for the task (1).
“While the Brady Review focused on broader mining activities, its findings resonate with mill relining. Vehicle accidents, machinery-related incidents, crush injuries, and falls from height – all which are risks identified in the Brady Review – are present during relining events."
Training matters on the ground
The mining industry's resource shortage and reliance on contractors for highly specialised, yet infrequent maintenance operations, like mill relining, also creates unique safety challenges. Diverse workforces can have varying experience levels, so safety practices can be inconsistent, while high turnover can hinder training continuity. Contractor reluctance to report safety concerns also further complicates matters. Professor Michael Quinlan spoke generally to this point in a 2023 article when he said there can be a complex chain of command and fear of job loss for contractors as key obstacles to raising safety concerns. This calls for greater collaboration between miners, contractors, equipment manufacturers, and regulators. Developing accredited and shared training standards, and addressing cultural barriers to reporting safety incidents, are crucial steps towards a more unified safety culture.
The intersection of safety and Environmental, Social, and Governance (ESG)
RME’s 40 years in the comminution industry means it has had a front-row seat to these challenges in mill relining. Our filmed safety studies consistently reveal significant opportunities for site safety improvement, from mitigating hazards with engineered solutions to addressing crucial competency and training gaps. Compliance is just the starting point. Ensuring RUSSELL Mill Relining Machine (MRM) operators are highly skilled, practice safe behaviours, are familiar with the latest technology and methods is paramount.
"Adequately trained supervisors are not merely a functional box to tick, but are an investment in lives, livelihoods, and communities. Preventing incidents that can shatter families aligns with RME’s core commitment to responsible mining. Delivering comprehensive operator training is more than just a safety measure; it is a pillar of our ESG responsibility."
Key aspects of MRM operator training and advanced technology familiarisation
Prioritising training for reline crew, MRM operators, and supervisors offers numerous benefits, including:
- Safe practices and skills: Equipping personnel with the knowledge and expertise to prevent and avoid unsafe practices and poor maintenance routines that can lead to incidents.
- Familiarisation with complex machinery: Ensuring operators are aware of their MRM’s specific configuration, and proficient with its systems, controls, recommended safe operating practices, and load capacity limits.
- Competent handling: Instilling competence in safe handling, liner placement, and release of liners, sway minimisation, and selecting the correct grapple attachment for various mill relining tasks—ensuring the protection of people, plant, and equipment.
- Emerging and advanced technology: Keeping operators informed and proficient in evolving mill relining processes, best practices, and new automation technologies that are enabling safer and faster relining from outside the mill.
"When safety is at stake, not all training programs are equal. Mining sites should seek accredited MRM operator training providers. Accreditation by independent regulatory bodies ensures adherence to reputable standards. When selecting a training provider, it is essential to ask for evidence of accreditations, quality certifications, and a proven track record of successful program delivery."
Why accreditation matters
Training certification plays a crucial role in improving mill relining safety for several reasons:
- Compliance: Courses ensure compliance with industry standards and regulations, creating a baseline of knowledge essential for safe mill relining practices.
- Risk mitigation: They address specific hazards and challenges, reducing the likelihood of incidents.
- Task-specific skills: They promote awareness of, and reduce risky operator behaviours, and instill task-specific competencies to prepare reline crew for the unique challenges of their role, and their role within the reline team.
- Assurance: Mine sites can be assured that they have taken all practicable steps to create a safe, secure and productive mill relining work environment.
Invest in safety excellence with RME Certified Training
RME’s Certified Training is developed in consultation with industry and user feedback. Courses are also certified with TAFE Queensland RTO No. 0275 and endorsed by the Australian Government’s Australian Skills Quality Authority (ASQA), guaranteeing quality content, regular audits, and continuous improvement. RME also offers ongoing support with refresher courses available for previously trained personnel. Courses are delivered by RME Certified Trainers in multiple languages. To date our training has empowered over 2100 personnel across 36 countries and all continents world-wide with safer more efficient mill relining practices.
A collaborative journey towards safer mill relining
Continually improving safety standards in mill relining requires a concerted effort to prioritise high quality training for MRM operators and supervisors. Partnering with accredited training providers empowers mine sites to build and develop site-specific expertise, boost reline efficiency, safeguard asset integrity, and minimise downtime.
This topic, however, raises an equally important point, and that is the role of mentorship. Mill relining technology is changing rapidly. The ‘RME Advanced Technology Mill Relining System’ means that commercial solutions ‘now exist’ to enable ‘safer relining from outside of the mill’. While these solutions leverage established and proven technologies, they still entail process shifts, which in turn demands a corresponding cultural transition.
"Establishing a mentoring program for on-the-ground reline crews in cooperation with technology suppliers, is crucial for the successful integration of new methodologies."
Beyond equipment mastery, this also cultivates a safety-centric culture. Mentorship programs impart hands-on guidance and expertise, fostering a safety-first mentality and adherence to optimal practices. This knowledge exchange is indispensable for optimising the benefits of both existing and new technologies. Additionally, the program serves as a conduit between suppliers and mine sites, facilitating open dialogue, problem-solving, and continuous improvement. RME, as the mentor, leverages these real-world site insights to ensure all users of the RME Mill Relining System globally benefits from enhanced safety practices. Ultimately, empowering reline crews through mentorship will significantly improve safety across the sector.
Together, we can make mill relining safer, one skilled operator at a time.
Click here to learn more about RME Certified Training for your operators and mill relining crews. And reach out to your nearest regional sales and support centre for more information on the RME Mill Relining Optimisation Program which has a mentorship program at its core.
1. Brady Review | Brady Heywood. Review of all fatal accidents in Queensland mines and quarries from 2000 to 2019 | By Sean Brady for the Queensland Government Department of Natural Resources, Mines and Energy | December 2019 [online] https://www.bradyheywood.com.au/brady-review/ . Available at: https://documents.parliament.qld.gov.au/tableOffice/TabledPapers/2020/5620T197.pdf
Content related to this article
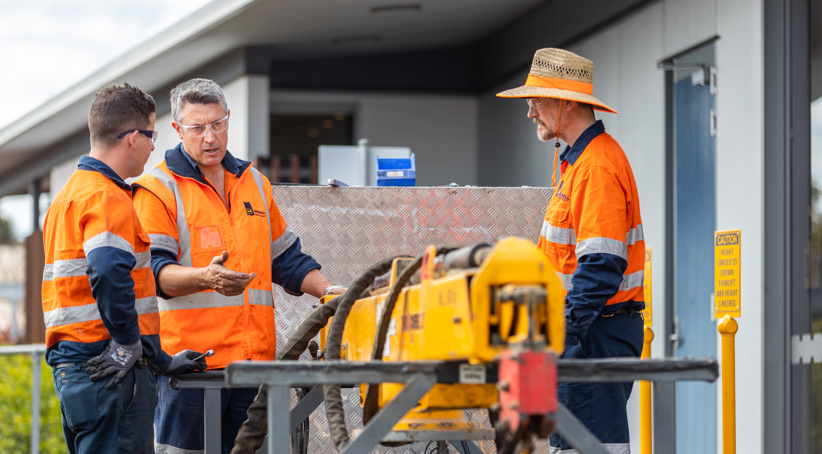
CERTIFIED TRAINING
When safety stakes are high, as they are in relining, partner with RME to deliver fully-accredited operator training. This will reduce the risk of incidents and improve safety.
Read More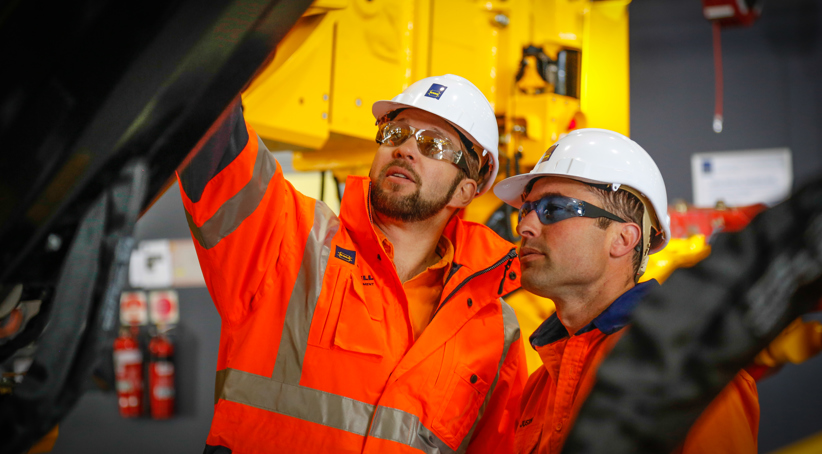
MILL RELINE DIRECTOR SAFETY
A MILL RELINE DIRECTOR Safety film study benchmarks your safety performance and provides practical risk reduction strategies for your next reline event.
Read More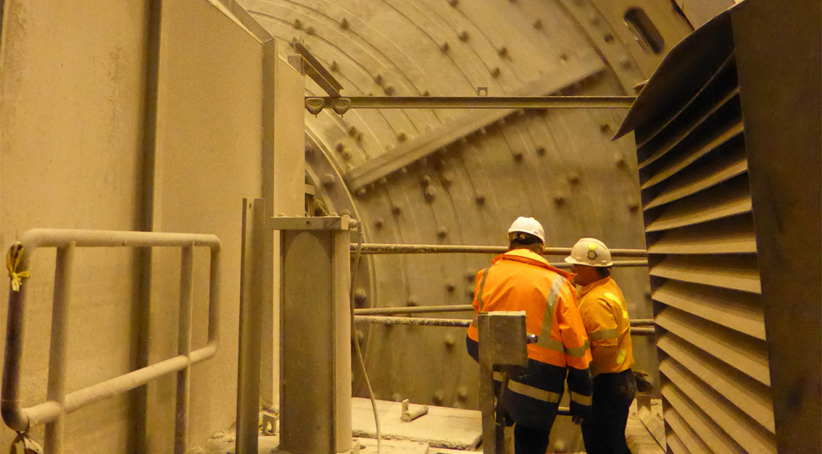
RME MILL RELINING OPTIMISATION PROGRAM
We can help you reduce shutdown duration, achieve maintenance predictability, eliminate risk and increase mill availability.
Read More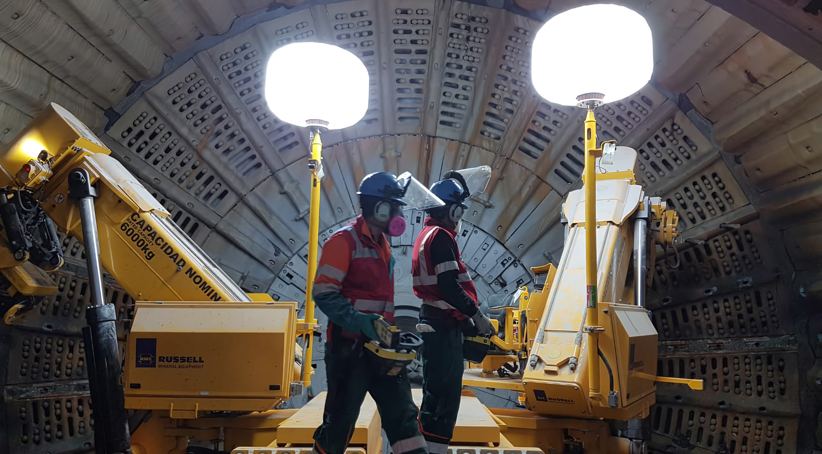
WE ARE HERE TO HELP
We ensure Customers have access to trusted OEM engineering know-how where and when they need it. Here's how to contact RME.