09 July 2024
THE DURABILITY DIVIDEND: Built-to-last reduces total cost of ownership
Invest in quality. Lower TCO. Improve ROI. Our commitment to robust manufacturing standards is also a sustainability principle! Read our blog to explore 10 reasons more mill operators trust the reliability and longevity of the RME Mill Relining System.
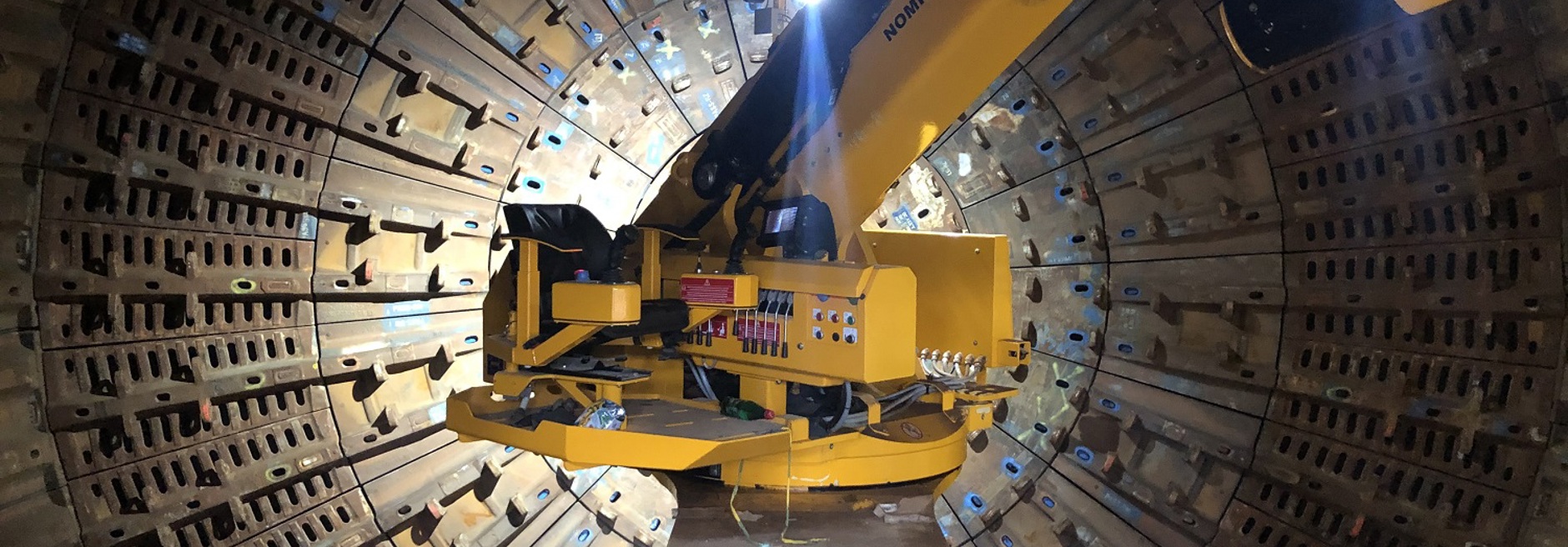
When it comes to mineral processing equipment, reliability and durability are non-negotiable. This is because unplanned downtime of production-related assets can incur significant financial losses for mill operators.
Furthermore, costs associated with premature heavy machinery replacements not only erase any short-term savings from a lower initial purchase price, but also contribute to a higher total cost of ownership (TCO) over the equipment's lifespan.
It is in this critical arena that RUSSELL Mill Relining Machines (MRMs) stand tall with a proven reputation for robust engineering. Backed by solid evidence of their exceptional performance and lifespan in the field, these machines are widely regarded as the epitome of reliability and longevity across the global mineral processing industry.
But how did RUSSELL MRMs earn this high regard and what sets them apart from the others?
Quality. The RUSSELL MRMs’ reputation is the result of the company’s 40-year commitment to precision-engineering and focus on quality manufacturing.
RME’s approach has always been to build solutions that endure demanding environments throughout every stage of the machine's lifecycle, from the initial custom-engineering and manufacturing processes, to after-sales asset support and site optimisation.
Since the introduction of our first RUSSELL MRM in 1990, we have continually raised the standard of engineering quality and machine functionality. Each evolution improves the mechanical, hydraulic, electrical and operational features that underpin unparalleled reliability, productivity, and safety.
“RME’s dedication to quality and durability is also a sustainability principle. It is typical and expected to see well-maintained RUSSELL MRMs exceed 20 years of service, minimising raw materials consumption through their exceptional longevity."
This translates to a lower TCO and higher return on investment (ROI) and is a testament to our steadfast commitment to designing and building quality machines that stand the test of time.
For these reasons, mill operators prefer to invest in a RUSSELL MRM, so in this blog, we explore some of the key criteria that supports their decision-making.
Here are 10 reasons why RUSSELL Mill Relining Machines are trusted for reliability and durability:
-
When you buy a RUSSELL MRM, you inherit 40 years of RME DNA, matured and strengthened through 570+ MRMs delivered. Mill relining is not just what we do – it is all we do. This singular focus translates into a clear advantage for our Customers. For four decades, we have led with original thought, pouring expertise and investment into inventing and ever-improving the industry's most progressive and reliable mill relining technologies. We continuously leverage this experience to optimise every stage of the relining process, working relentlessly to eliminate risks to reline crews, reduce reline time and improve mill availability. Furthermore, RME's team of experts possesses deep knowledge and OEM experience in this specialised field. This expertise allows us to custom-engineer solutions for each specific mill’s needs. Every RUSSELL MRM is built on this foundation, guaranteeing solutions that are both time-tested and cutting-edge. Customers benefit from the proven reliability of the past while gaining access to the innovations of the future.
-
The future of mill relining is rapidly evolving with roboticisation poised to revolutionise the process by reducing and eliminating hazardous and manually-repetitive tasks. Mill operators can now control risks inside the mill by relining from outside the mill, improving both reline safety and speed. RME is both leading this change and making it accessible. Not only does our modular technology platform have future-proofing built in, our commercially-available RME Advanced Technology Mill Relining System allows mine sites to adopt these methods easily, and progressively, during planned maintenance windows. This flexibility ensures mill operators avoid being ‘locked-in’ to equipment that quickly becomes outdated. As new solutions emerge, our systems are integration-ready. RME also recognises that not every operation requires a fully-automated system, so our modular approach also allows for partial adoption of RME INSIDEOUT Technology. For example, even existing RUSSELL 7 and 8 MRMs in-the-field can be retrofitted with an innovative tool that eliminates hazardous manual liner slinging, and with it, the need for crew inside the mill during muck-out. This dramatically improves safety at a cost-effective price point. Having this ‘optionality’ ensures all mills can secure significant improvements risk exposure and relining efficiency, while extending asset utilisation, lifespan and ROI.
-
Mill operators can extend and optimise the performance of their mill relining equipment through RME’s extensive range of proprietary safety and productivity accessories and upgrades. These upgrades go beyond basic operation to enhance system reliability and strengthen machine durability. Upgrades like fit-for-purpose grapple attachments and asset protection gear to slow the rate of machine wear and tear and extend your asset’s operational life. Automation features and control upgrades work together to improve safety and ensure the RUSSELL MRM operates at peak performance for longer.
-
RME’s commitment to quality manufacturing and machine longevity starts with the materials we use. Our selection processes go simply beyond meeting standards – we source high-quality materials that will endure years of rugged operation and withstand harsh mineral concentrator plants. This meticulous approach extends throughout the manufacturing processes, incorporating advanced techniques and superior finished treatments with protective costings. The results? Machines that sustainably deliver decades of reliable service. Of course, proper care plays a role too. With regular inspections and preventive maintenance, RUSSELL MRMs will perform for many years to come. (Customers can read our ‘Best practice mill liner handler care and maintenance eBook’ for practical advice on extending the life of your RUSSELL Liner Exchange Machine)
-
Mill operators cannot afford mill relining equipment failure mid-reline, so machine structural integrity is a paramount consideration. All RUSSELL MRMs structural materials and steels are certified, and their source are recorded. Complete records are retained by RME and available to our Customers at any time. All welding processes are prequalified and RME’s welding quality is legendary, both in its integrity and surface finishing. All machining processes are quality assured up to and including high-precision components, which are assessed by RME’s certified coordinate measuring machine which has micron accuracy.
-
RUSSELL MRMs robust hydraulic systems prioritise both operator safety and machine reliability. The foundation lies in high-quality, ISO-standard components that ensure system integrity. To further safeguard operators and machinery, RME has cleverly eliminated the presence of visible hydraulic hoses in the areas most susceptible to impact. Leveraging our 40 years of OEM (Original Equipment Manufacturer) expertise, RUSSELL MRMs also incorporate multiple levels of design redundancy across all the hydraulic control systems. These protect against potential fault and failures, resulting in more robust and reliable control systems.
-
RUSSELL MRMs own the confidence of hundreds of mill operators because of their rigorous electrical safety standards and adherence to international regulations. Every machine is meticulously engineered and manufactured to meet the specific electrical codes and standards as required. Our rigorous power electrics design process incorporates multiple layers of protection against electrical faults and failures. This includes using well-tested components and implementing alternate routing or separation strategies for critical circuits. Furthermore, we follow strict "Electrical Equipment for Machines" verification procedures to ensure all aspects of electrical integrity are addressed. Detailed documentation is maintained for each machine, providing a clear record of the design and safety measures implemented.
-
The intelligent electronic control design of all RUSSELL MRMs places additional ticks in the ‘safety’ and ‘machine reliability’ boxes for mill operators. We employ well-established safety principles and components to minimize inherent risks associated with electronic controls. Our development process rigorously addresses both random and systematic failures in critical controls like unexpected motion and load release. This proactive approach ensures exceptional reliability and minimises downtime. Redundant or dual-path circuits with alternate routing or separation strategies are implemented to resist common cause failures. This redundancy strengthens the overall system, maximising equipment performance and reliability.
-
The safety of grinding mill relining personnel relies upon the engineering and manufacturing integrity of the equipment they operate. RUSSELL MRMs are custom-engineered and manufactured by our expert teams at our ISO-certified facilities in Australia. Not only do RUSSELL MRMs meet all necessary codes for the country in which they will operate, but they will exceed these standards with RME’s own rigorous structural integrity standards. This ensures exceptional performance and durability, even in the harshest of environments and variable operator handling practices.
-
Lower asset lifecycle costs are assured for mill operators when equipment is genuinely built-to-last and properly maintained. RUSSELL MRMs are required to survive life in mineral concentrators where acidic process waters and airborne contaminants present significant corrosion hazards and risk. All fabricated components are free from weld splatter, are grit-blasted and painted independently, inside and out, prior to machine assembly. All smaller parts are either stainless steel or plated, ensuring high performance even in the harshest of environments.
The ability to eliminate hazardous risk and increase mill availability are ‘must-haves’ for every mill operator. RME’s quality engineering empowers sites to achieve both, while also lowering TCO over longer equipment lifespans.
What’s more, the RME Mill Relining System isn't just a liner handler and or a knock-in hammer – it's a comprehensive suite of technologies designed to optimise safety and efficiency at every stage of this critical maintenance process.
Our commitment to quality also extends to 24/7/SERVICE asset support, certified operator training that prevents wear and tear from accidental misuse, and certified OEM parts that ensure optimal performance and warranty protection.
"This comprehensive approach, proven over 40 years of innovation, delivers both safety and peace of mind, and grants mill operators unparalleled opportunities to improve concentrator performance – visibly, defensibly, sustainably."
To find out more contact your nearest RME team. We are here to answer questions, offer advice and help our Customers discover and optimise the most appropriate mill relining system for their mine site.
Content related to this article
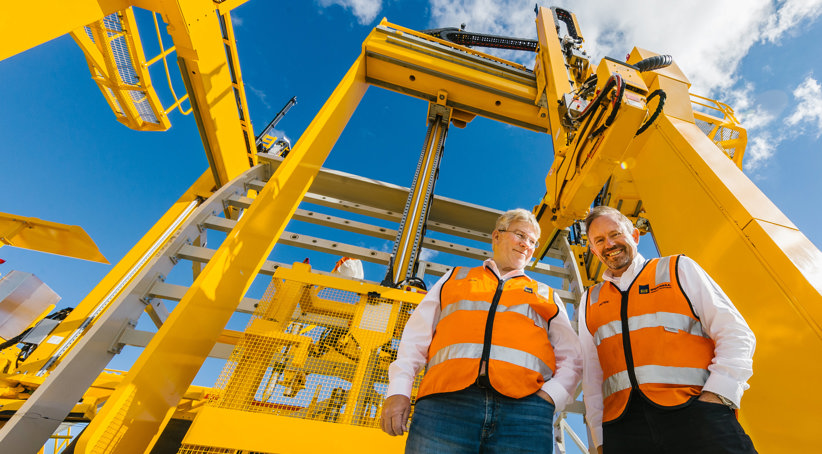
WHAT WE DO
Trusted for almost 40 years as the global leading manufacturer and supplier of fast, reliable, safe, mill relining technologies, asset support and optimisation services.
Read More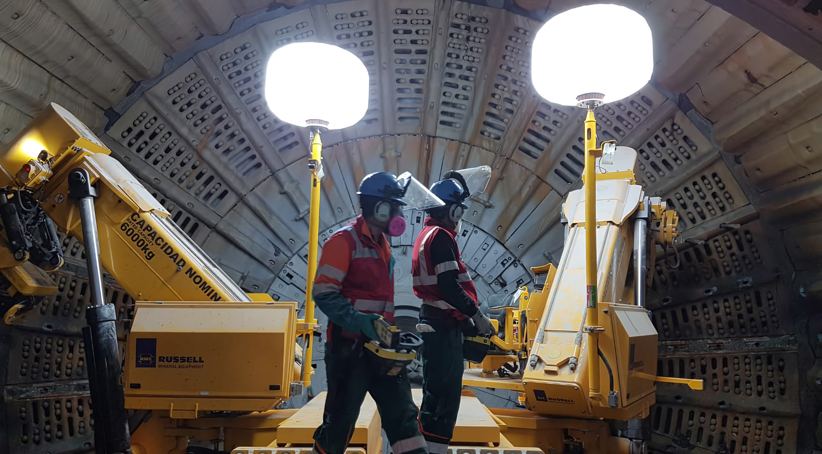
RUSSELL LINER EXCHANGE MACHINES
The trusted choice for mill operators globally. Our expanded, higher-performing range – from <400 kg to 10 tonne capacities – ensures fast, reliable, safe mill relining is available to every mine site.
Read More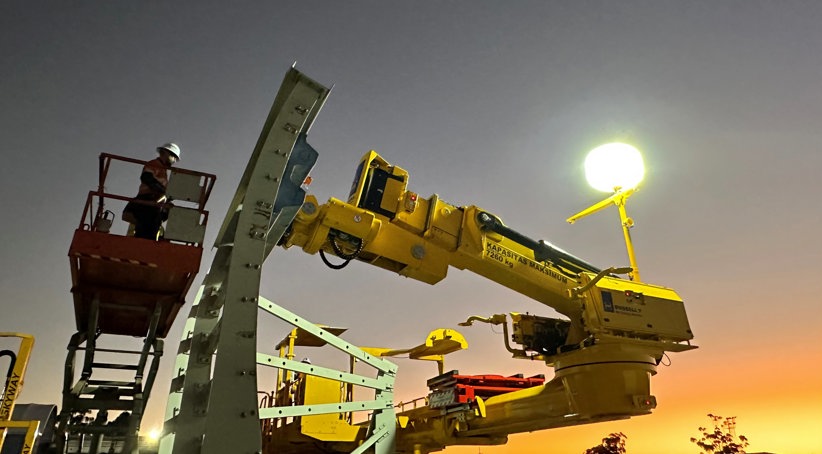
RME ADVANCED TECHNOLOGY
Our relentless pursuit to improve safety and productivity has driven us to engineer a future where relining is performed safely from outside the mill – at faster speeds than ever before.
Read More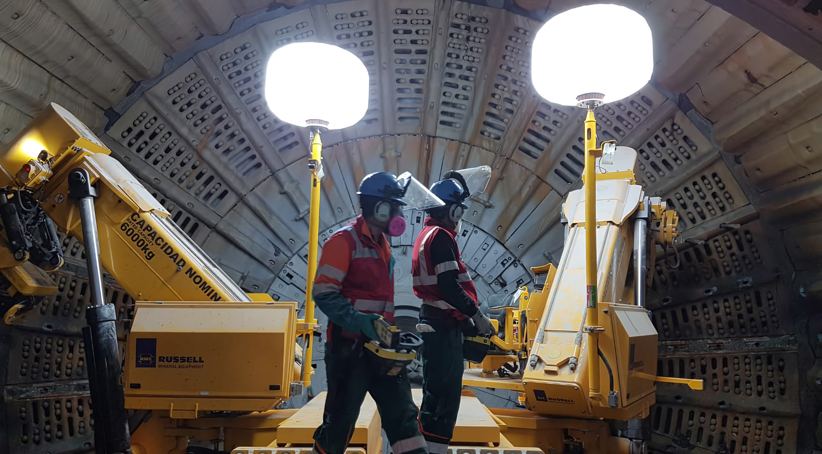
WE ARE HERE TO HELP
We ensure Customers have access to trusted OEM engineering know-how where and when they need it. Here's how to contact RME.