02 September 2020
RME announces the new THUNDERBOLT MAGNUM Recoilless Hammer range
RME is announcing the official release of its fourth-generation liner removal tool – the THUNDERBOLT MAGNUM Recoilless Hammer.
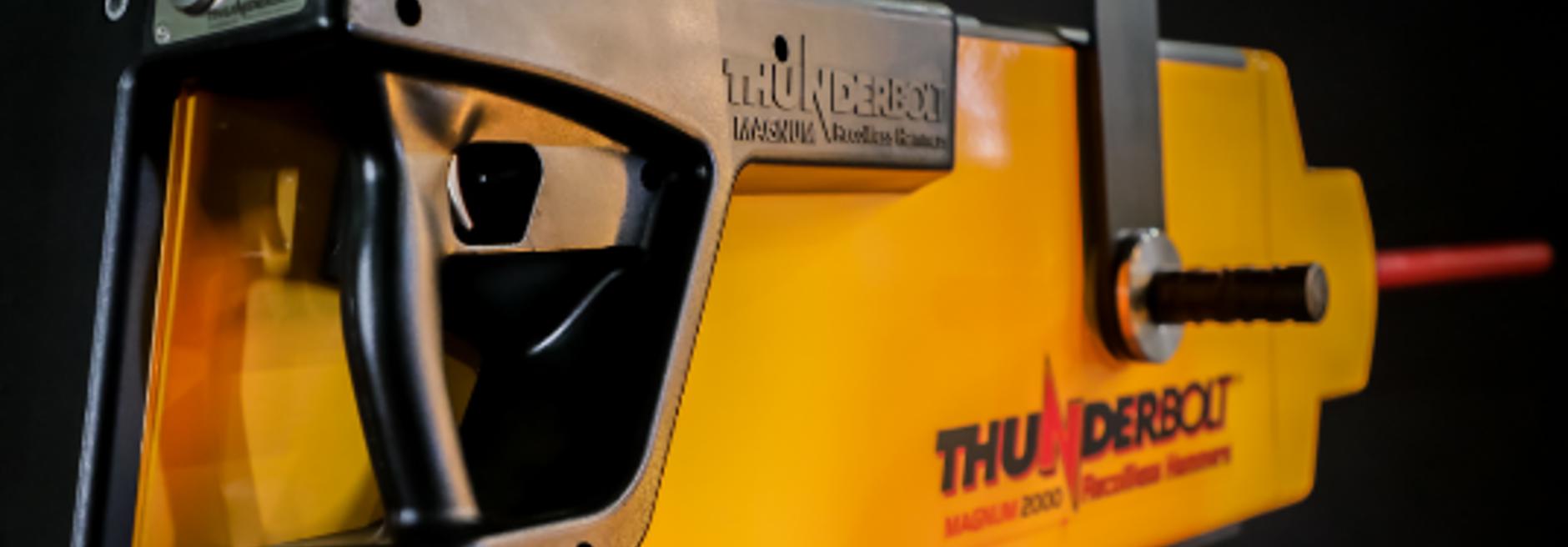
RUSSELL MINERAL EQUIPMENT celebrates official release of THUNDERBOLT MAGNUM Recoilless Hammer range with exclusive Customer offer.
THUNDERBOLT MAGNUMs deliver unrivalled force and momentum with unmissable precision to improve relining knock-in speed, safety – and mill availability.
HIGHLIGHTS:
- RME adds two new models – THUNDERBOLT MAGNUM 2000 and THUNDERBOLT MAGNUM 1000 – to its now six-strong THUNDERBOLT Recoilless Hammer range
- Introductory special bundle offer – save 20% on ‘THUNDERBOLT MAGNUM Precision Pack’ orders placed before December 31, 2021 and delivered before June 30 2022
- New models deliver the industry’s highest force to 2000 joules per blow1 and fastest sustained speed to 160 blows a minute2
- Operator-selectable ‘MAGNUM Mode’ power for precision performance and control
- Ground-breaking 90% dry fire shock reduction minimises machine stress and operator fatigue3
- Extended service intervals by 150% at 100,000 blows3 for greater uptime and reliability
RUSSELL MINERAL EQUIPMENT (RME), the world’s leading manufacturer and supplier of mill relining solutions to the minerals processing industry, is marking the official release of its fourth-generation recoilless hammer with a special introductory bundle offer for its Customers – the ‘THUNDERBOLT MAGNUM Precision Pack’.
This all-inclusive pack offers incredible value and includes both the THUNDERBOLT MAGNUM 2000 and THUNDERBOLT MAGNUM 1000 Recoilless Hammers (the latter included at no cost), the THUNDERBOLT MAGNUM Power Pack (swappable between both models), the higher-reach THUNDERBOLT MAGNUM Mobile Jib (useable across the entire THUNDERBOLT range), as well as a comprehensive set of ancillaries and spares. With the THUNDERBOLT MAGNUM 1000 HAMMER included at no cost, the ‘THUNDERBOLT MAGNUM Precision Pack’ represents 20% off the standard price of the individual equipment purchased separately. This exclusive offer is available immediately on all orders placed before December 31, 2021, with a delivery date prior to June 30 2022
“We know from 35+ years partnering with Customers on mill relines, there’s no one-size-fits-all solution to worn liner bolt knock-in. In fact, industry benchmark operations will use the hardest hitting hammers for difficult-to-dislodge bolts at discharge end and breaking-in on the first inch, then swap to a high repetition hammer for ploughing through shell lifter liners”, said Christian Kramer, THUNDERBOLT Product Manager, RME.
“This is why we’re excited about the new THUNDERBOLT MAGNUM Precision Pack. Not only do MAGNUMs hit harder and faster than the previous range, but also, when paired together, they provide four (4) selectable levels of power for an even greater ability to select precisely the right level of power forguaranteed precision whatever the specific knock-in application. Combined they’ll reduce mission-critical relining knock-in hours, especially on high-wear relines, which means higher mill availability.”
In developing the new THUNDERBOLT MAGNUM Recoilless Hammers, RME applied 10,000+ hours of research and development using Customer-led design principles, to deliver quantifiable upgrades in strike energy, speed, serviceability and operator safety. The range sports two ergonomically designed Hammers with each offering Customers a unique advantage to shorten the mill reline knock-in phase.
Designed specifically for large and medium SAG and AG mills, the mighty THUNDERBOLT MAGNUM 2000 delivers an incredible 2000 joules per blow 70 times a minute to plough through the toughest of knock-in phases, such as tough, stuck and deeply-wedged liner bolt bolts at a mill’s discharge end or breaking-in shell liners on the first inch, with ease. In initial commercial trials, the MAGNUM 2000 has even demonstrated the ability to knock-in peened liners without resorting to dangerous and time consuming lancing.
The THUNDERBOLT MAGNUM 1000 will excel in any reline environment across SAG, AG and ball mills small, medium and large. Its accelerated strike rate up to 1000 joules 140 times a minute outperforms every other liner removal tool when it comes to work-rate speed and safety.
“When the first-generation THUNDERBOLT was released in 1997, it was a game changer for the minerals processing industry,” said John Russell, Founder and Executive Chairman, RME. “As the world’s only true recoilless hammer, it replaced hazardous manual methods and unfit-for-purpose tools which seriously jeopardise reline efficiency and operator safety. The fourth-generation THUNDERBOLT MAGNUMs not only build on RME’s fundamental fast-reliable-safe principles, they improve on them in every way. We’re so pleased to give our Customers early and exclusive access to this incredible time-saving mill relining technology through the new THUNDERBOLT MAGNUM Precision Pack.”
Additional feature highlights exclusive to the THUNDERBOLT MAGNUM range include:
Intelligent programmable power for precision performance
THUNDERBOLT MAGNUMs usher in a new ‘MAGNUM Mode’ which allows operators to program strike energy and speed for greater safety, precision and control. This selectable power also reduces the risk of high-velocity bolt projectiles, which can damage mill relining equipment and put crew at-risk, at the end of liner bolt knock-in.
Extended service intervals
Service intervals on the new MAGNUMs have increased by 150% to 100,000 blows through ingenious engineering and the highest manufacturing standards. Longer life components, improved component accessibility, smarter diagnostics, and improved shock absorption reduces maintenance requirements for greater equipment uptime and reliability.
Smarter condition monitoring
New THUNDERBOLT MAGNUM Power Packs feature new sensors and diagnostic controls for improved performance monitoring and maintenance optimisation. Optimal tuning and blow data is now stored within the hammer for accurate operational insights and better lifecycle decision-making. The new MAGNUM Power Pack is swappable between the MAGNUM 1000 and MAGNUM 2000 Hammers for efficient total cost of ownership (TCO).
Designed to provide the most comfortable, and safest operator experience
Improved ergonomics and a 90% reduction in recoil dry fire shock minimises both machine stress and reline crew fatigue. Hydraulic systems have also been redesigned for improved operational safety and use. A dual-action contact trigger safety mechanism eliminates risk of accidental firing. Streamlined operator inputs and improved mechanical and electrical controls protect crew working around the hammer and enhance the safety of mill reline operations.
Safer steadier suspension
With this product launch comes a new higher-reach THUNDERBOLT MAGNUM Mobile Jib with greater clearances, upgraded stability and a safety brake. This higher reach means access to more rows of liner bolts and can reduce the number of inching movements and inching time per reline. The MAGNUM jib can also be used across the entire hydraulic THUNDERBOLT Recoilless Hammer range.
About THUNDERBOLT Recoilless Hammers
Powerful, productive, reliable, THUNDERBOLT Recoilless Hammers set the global standard for the fastest and safest method for worn liner removal. Since 1997 THUNDERBOLTs have been replacing manual methods such as heavy, manual sledge hammers, battering rams and unfit-for-purpose rock breakers – all of which undermine mill relining speed and safety. Preferred by mine management and reline crew, THUNDERBOLTs guarantee a continuous precise high-energy strike with minimal recoil to the operator. With six models in the range offering forces from 250 to 2000 joules per blow, and 60 to 160 blows per minute, there is a knock-in solution for every mill type and liner application. The THUNDERBOLT Recoilless Hammer is the mill relining industry’s best-selling liner and bolt removal tool with 860+ sold worldwide to date. Renowned for equipment reliability and longevity, THUNDERBOLTs offer lower Total Cost of Ownership (TCO) over asset life. Visit www.rmeglobal.com/thunderbolt.
About RUSSELL MINERAL EQUIPMENT
RUSSELL MINERAL EQUIPMENT (RME) revolutionised the global mill relining industry with the introduction of the first mechanised mill relining machine in 1985. Since then, the RME Mill Relining System has quartered its Customers’ time-to-reline and eradicated a great many safety issues. This same pursuit drives the development of RME INSIDEOUT Technology – an advanced suite of solutions proven to improve mill availability and remove people from risk inside and outside the mill – representing a safety world-first. Headquartered in Queensland, Australia, RME serves over 380 mine sites worldwide through 11 Regional Service Centres in all major mining markets globally. Visit www.rmeGlobal.com.
Related articles
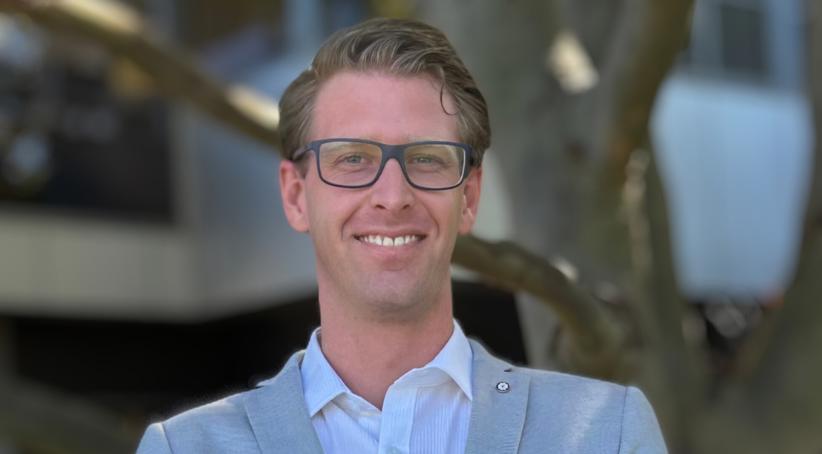
RME appoints General Manager of Engineering, Simon Thompson
RME announces today the appointment of a new General Manager of Engineering, Simon Thompson, ensuring RME continues build it's market-leading position globally.
Read More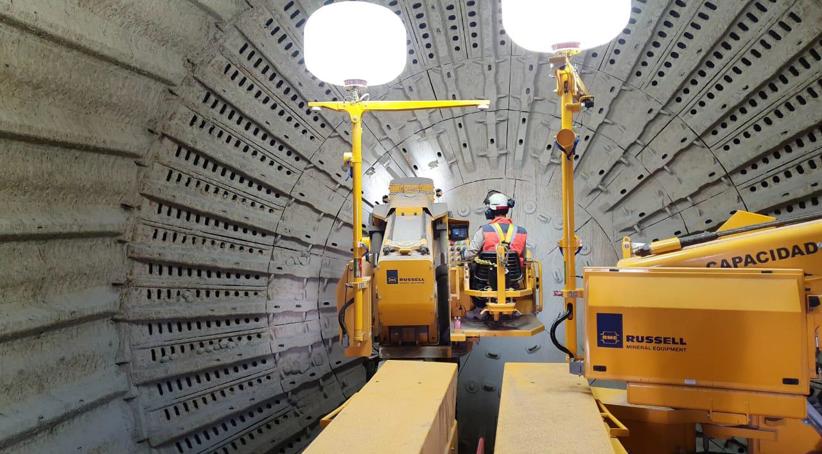
Best practice mill liner handler care and maintenance eBook
When safety, downtime and mill availability are at stake, it pays to do things by the book.
Read More