05 March 2015
RME achieves cost savings for customers with simulation-based approach
RME speaks with Daniel Gleeson of International Mining about how a simulation-based approach utilising MILL RELINE DIRECTOR helps customers achieve cost savings.
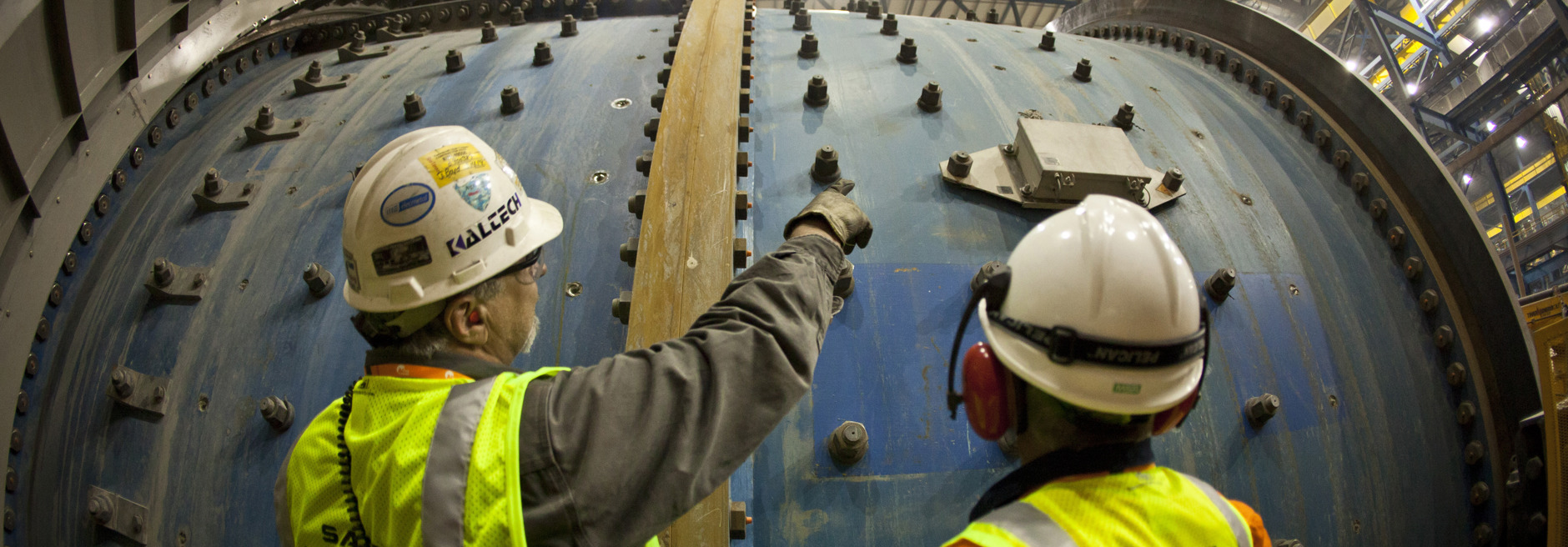
One of the key maintenance activities undertaken at a mineral processing site is relining of grinding mills. This process requires lengthy shutdowns of the grinding mills, costing vast sums of money through lost productivity. Undertaken two to three times a year on average, a typical reline process can take between 50 and 100 hours, with each hour of lost production costing between A$50,000 and A$200,000 in revenue. Reducing reline time by one day can recover millions of dollars in revenue lost through inefficient processes and under-used or inappropriate equipment.
As part of RME's commitment to improve the performance of our customers’ mineral processing concentrators, we have invested in the optimisation of the overall relining process as part of our service offering. “By looking beyond just the equipment they supply and taking a holistic view of their customers’ relining process, we are able to demonstrate how the relining activities could be best organised and complimented with appropriate products and services, resulting in greatly enhanced productivity and significant cost reductions for customers.”
Read the rest of Daniel Gleeson's article at International Mining.