14 May 2024
Optimising liner design and mill relining for improving concentrator throughput
Read our blog exploring recent research in comminution and discover how liners designed for performance, combined with faster, safer mill relining technology can boost process efficiency.
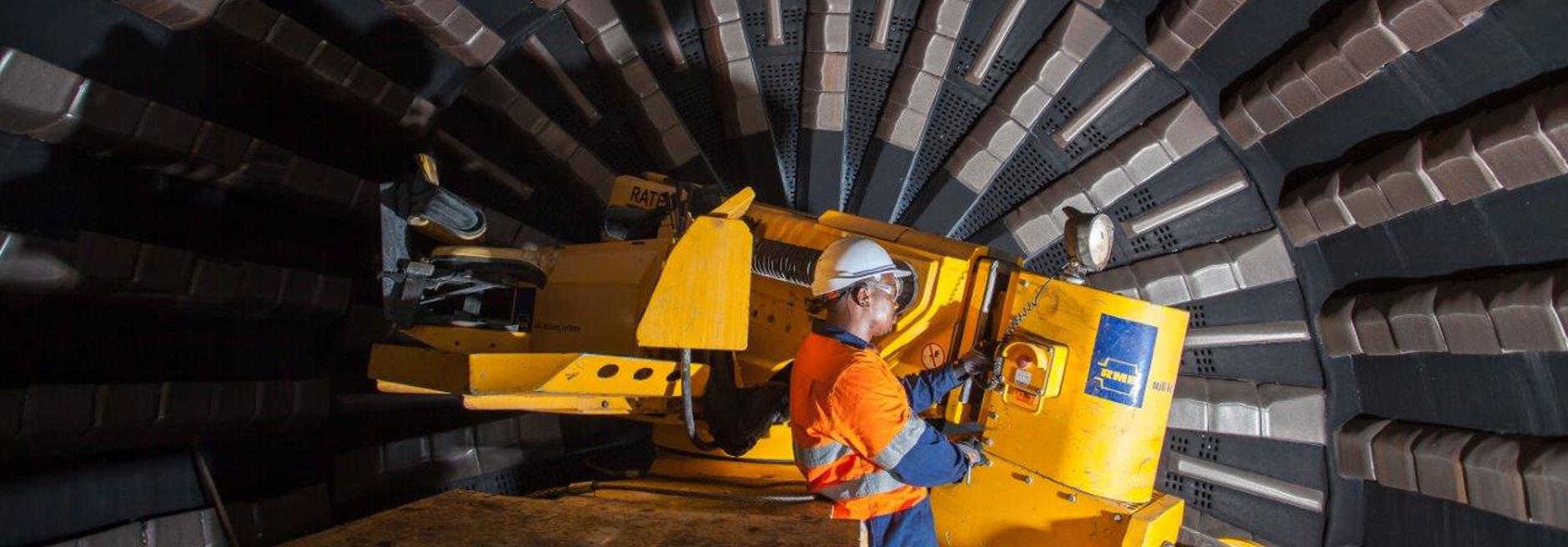
The Engineering and Mining Journal recently featured an excellent piece by Carly Leonida entitled 'Making milling and grinding more efficient'. The article highlighted current research in comminution aimed at enhancing process efficiency.
In the mining industry, semi-autonomous (SAG), autonomous (AG) and ball mills are very much the workhorses when it comes to grinding operations. The technology excels in reducing ore size and achieving high throughput rates with a reasonable degree of process scalability and flexibility. Overall, they do a 'very fine job' of it.
However, hard rock mineral concentrators are also significant consumers of energy to turn the mill, and steel media to grind the ore. With fewer high-grade ore deposits available for development, the average ore grades available to feed concentrators are declining. Lower ore grades often necessitate higher “run-of-mine” (ROM) throughputs – increases in the amount of raw material that needs to be processed to achieve the same amount of metal yield, which is increasing the energy demands for grinding.
Improving the energy efficiency of this process is a collective challenge for our industry, and we applaud initiatives like the ones mentioned in the article working to address this.
RME shares this perspective and would like to highlight another aspect from a section in the article which discusses liner geometry. We've long recognised the economic links between liner design, mill relining, throughput, and operational efficiency.
Back in 2006 RME’s Founder, John Russell, first explored the potential of optimised liner design for metallurgical and commercial performance and with faster relining practices to enhance throughput in a MetPlant research paper titled ‘Advanced Grinding Mill Relining Methods’.
Let's unpack this a little further.
The Liner Challenge: Balancing Wear and Performance
The primary function of a grinding mill’s liners is to protect the mill shell from the harsh milling environment, and to deliver energy to the charge to facilitate the grinding process.
However, the Achilles heel in the mill operation, is that the aggressive mill operating environment wears the liners out, necessitating regular replacement at considerable labour and lost production costs during the shut-down.
As a result, many liner designs will often prioritise extended lifespans to minimise relining frequency, which is achieved by designing thicker shell plates and higher and thicker lifter bars.
“In recent years, several engineering studies have shown that in some operating grinding mills, these thicker designs may not be optimal, and that they may be underperforming for a considerable portion of their lifespan, impacting mill productivity."
One reason for this is that when new, thick liners are used, mills are often operated at reduced speeds for the first few weeks after a reline, lowering throughput. This is necessary, because at full rotational speeds the steeper face angle of the new liner results in a different trajectory that over-throws the ore and media to impact directly onto the other liners, causing excessive wear and potentially cracking the liners. Using thicker liners designed to maximise life potentially exacerbates this issue, because it can extend the length of time that the mill must operate at this slower speed.
Then, towards the end of the liner life, the mill’s ability to deliver energy to the charge decreases when the lifters are worn, even though the mill is operating at maximum speed. This is because the liners’ worn contours are not able to lift the charge as effectively, again impacting throughput.
Performance-optimised liners
Various researchers have explored the concept of designing liners for performance rather than life. This approach aims to eliminate the low-performance periods at the start and end of liner life.
At last year’s SAG Conference in Vancouver, Canada, Ndimande, C. B., Hilden, M. and Yahyaei, M. presented findings in their 2023 paper entitled: 'Evaluating throughput benefits and safety aspects of mill liner design for performance'. Their paper built on previous research which has explored the concept of designing liners for performance rather than life (Toor, 2011; Toor et al. 2013; Yahyaei et al. 2015) and showed how three different operations would benefit from the concept, to slightly different degrees, depending upon the properties of the ore and mill operating practises.
However, the hesitation to adopt performance-optimised liners, despite their potential to eliminate low-throughput periods, often stems from concerns about a shorter liner lifespan. More frequent liner replacements are perceived to translate to increased downtime, which can be a risk to production and profitability. Mill relining’s inherent hazards have also historically disincentivised mine sites from increasing its frequency.
RME Advanced Technology Mill Relining System
RME has focused on delivering this improvement through new mill relining technologies and robotics which enable significantly faster and safer liner exchange. And with faster relining, mill operators can overcome the barriers to adopting performance-optimised liners and achieve greater throughput.
“Imagine ‘pit stop’ relines – a future where automation expedites the process while also improving worker safety."
Key benefits of this technology include:
- Significantly enhanced safety: Automation removes operators out of harm's way, and even from inside the hazardous mill environment.
- Predictability, precision and speed: Robotics ensure consistent, optimal liner exchange so operators can maximise mill availability and grinding efficiency throughout the liner lifespan.
- Reduced Downtime: Faster turnaround times mean the mill spends less time idle and more time producing.
Pinpointing the best methods for mill relining optimisation
Relining optimisation, however, goes beyond liner design alone.
Numerous factors and their interplay influence the efficiency of the process, and these can vary significantly across mills and sites. This complexity can make it challenging for operators to identify the optimisation methods that will deliver the highest commercial gain.
“RME's MILL RELINE DIRECTOR (MRD) helps navigate this complexity. This specialised engineering service involves filming and analysing mill relining events using Discrete Event Simulation (DES), and considers factors like liner design, plant layout, relining processes, equipment choices, and even crew performance."
MRD builds digital twins of mills and relining events to benchmark performance, simulate different scenarios, predict relining times, and demonstrate potential economic benefits of making changes. Mine sites, and mill and liner suppliers increasingly seek after this capability.
RME’s independent Liner Interface Assessments identify can also address potential liner fitment issues with RME equipment before manufacturing, ensuring a faster, safer and reliable relining experience.
Ready to unlock increased mill productivity and safety? Reach out to RME!
Content related to this article
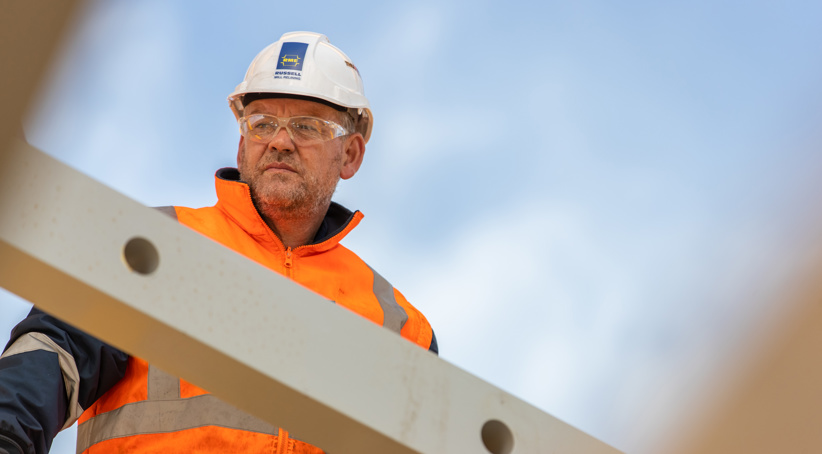
MILL RELINE DIRECTOR
MILL RELINE DIRECTOR (MRD) discrete event capture, analysis and 'digital twin' simulation provides clear line of sight into the complex process of mill relining.
Read More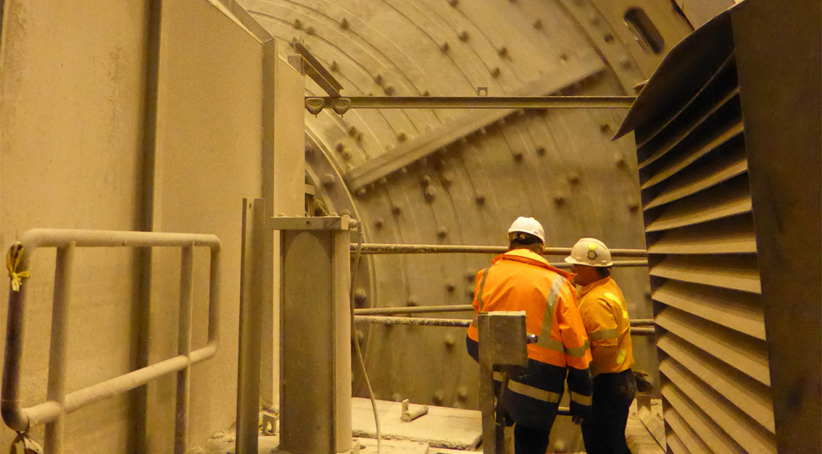
RME MILL RELINING OPTIMISATION PROGRAM
We can help you reduce shutdown duration, achieve maintenance predictability, eliminate risk and increase mill availability.
Read More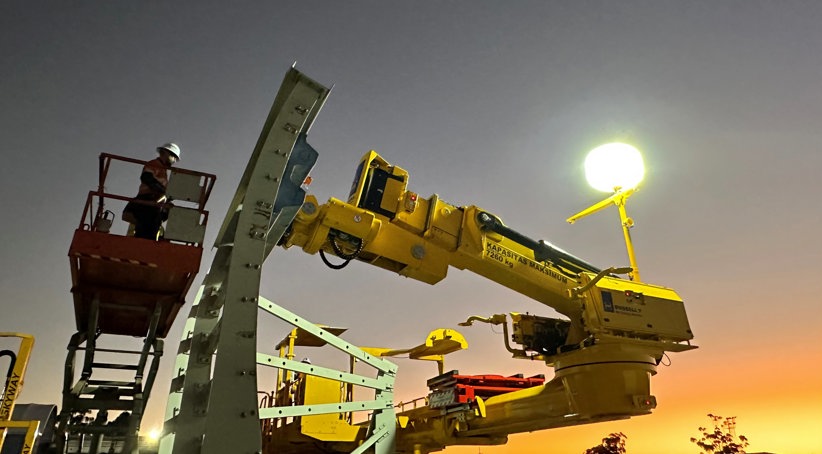
RME ADVANCED TECHNOLOGY
Our relentless pursuit to improve safety and productivity has driven us to engineer a future where relining is performed safely from outside the mill – at faster speeds than ever before.
Read More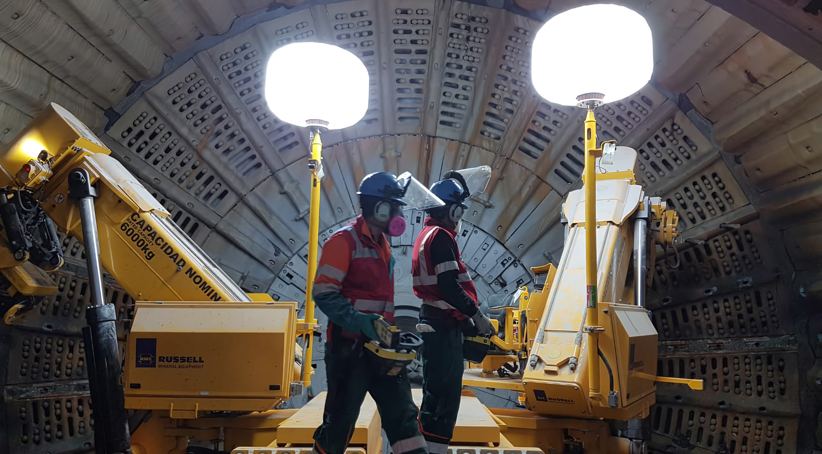
WE ARE HERE TO HELP
We ensure Customers have access to trusted OEM engineering know-how where and when they need it. Here's how to contact RME.