29 mayo 2025
Cómo la automatización está transformando el cambio de revestimientos: Lecciones de la GRX25
El Director de Ingeniería de RME, Simon Thompson, recientemente realizó una elocuente presentación en la GRX25 acerca de cómo la automatización está transformando la seguridad y la eficiencia del cambio de revestimientos. Enfatizó que, si bien la mecanización ha mejorado considerablemente la seguridad, los riesgos se mantienen, y RME está redoblando los esfuerzos para generar soluciones para eliminarlos.
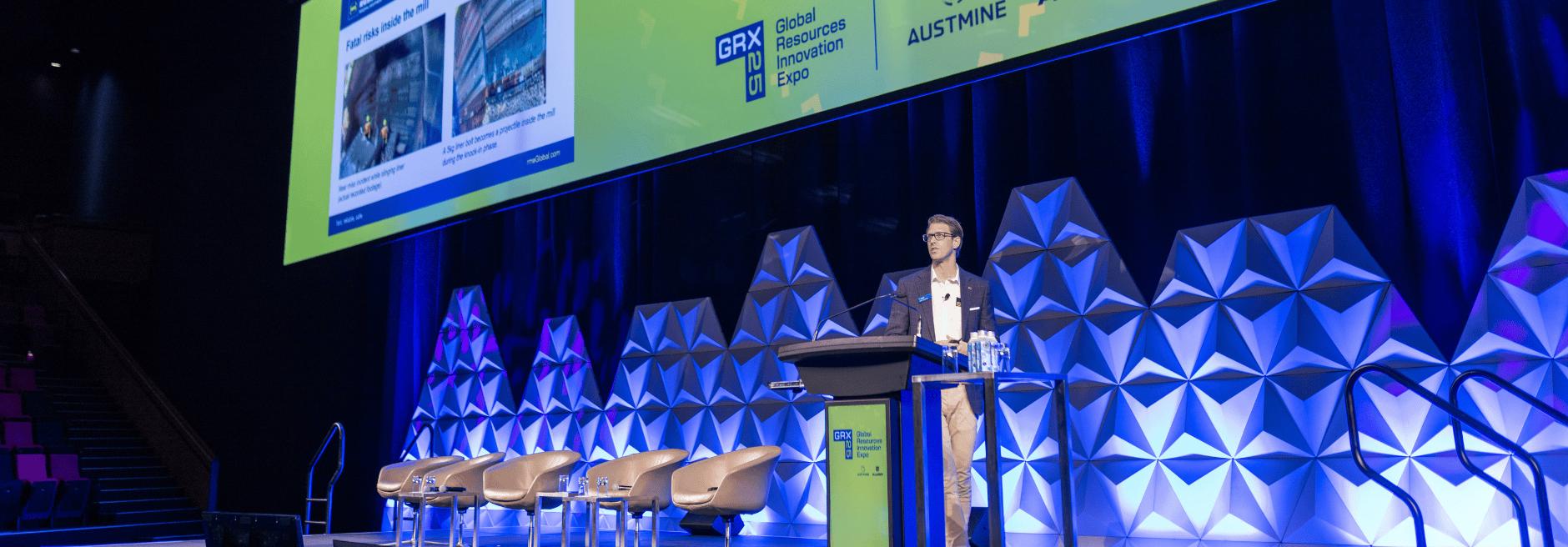
La Global Resources Innovation Expo (en español, Exposición Global de Innovación en Recursos, GRX25), realizada por Austmine y AusIMM en Brisbane del 20 al 22 de mayo de 2025, reunió a los líderes de la industria para explorar los avances en innovación, tecnología y sustentabilidad de la minería.
Durante el primer día de la conferencia, el Director de Ingeniería de RME, Simon Thompson, realizó una elocuente presentación, en palabras de Austmine, que exploraba el papel creciente de la automatización el aumento de la seguridad del cambio de revestimientos.
Simon Thompson recientemente fue nombrado Director de Ingeniería de RME, lo que fortalecerá la posición de la empresa como el fabricante de equipos originales de sistemas para revestir molinos más confiable del mundo y líder en tecnología avanzada.
Su presentación, "Automatización del cambio de revestimientos del molino: Aplicando las lecciones aprendidas", basada en un reciente artículo de conferencia de RME (créditos al autor en la parte inferior), exploró cómo la automatización está eliminando los riesgos fatales y mejorando la productividad en las compañías mineras que adoptan estas tecnologías, y cuáles han sido las lecciones valiosas de la travesía de la optimización.
Por qué la automatización es esencial para el cambio de revestimientos
El cambio de revestimientos mecanizado, concebido primero por el Fundador de RME, el Dr. John Russell, hace cuatro décadas, luego comercializado y madurado por la experiencia en ingeniería de la empresa, mejoró considerablemente la seguridad y la eficiencia del mantenimiento de los molinos. Al reducir la manipulación manual, permitió el uso de corazas más grandes y pesadas, lo que disminuyó la cantidad de piezas, acortó el tiempo que toma cambiarlas y mejoró la disponibilidad del molino. Sin embargo, pese a este progreso, los riesgos fatales permanecen.
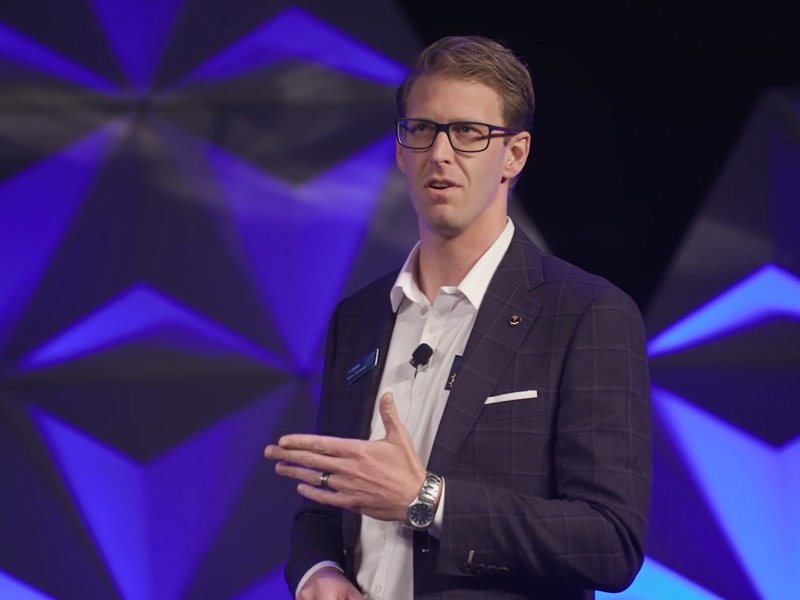
"En el cambio de revestimientos mecanizado, los riesgos residuales siguen existiendo: hay espacios confinados, trabajo en alturas y el desafío de trabajar bajo cargas suspendidas de varias toneladas cerca de la planta y equipos móviles. La automatización es el siguiente paso: saca a las personas del interior del molino y las aleja del riesgo fatal de las actividades del cambio de revestimientos".
La presentación de Simon incluyó filmaciones de la vida real que ilustraron los peligros del cambio de revestimientos que se mantienen. Un clip mostró la caída de una coraza de tres a cuatro toneladas debido a prácticas de eslingado incorrectas, que apenas esquivó a la cuadrilla que se encontraba trabajando abajo sobre la carga (el piso del molino). Otro mostró cómo un perno de revestimiento de cinco kilos se convertía en un proyectil durante el botado, que sería casi imposible de esquivar, destacando la imprevisibilidad de los peligros en el interior del molino.
"Estos clips muestran los peligros reales que enfrentan los operadores. Reafirman el por qué la automatización, que saca a las personas de dentro del molino, es esencial para eliminar los riesgos fatales y aumentar la seguridad de nuestras cuadrillas".
Las mejores prácticas de antaño, no son las mejores de ahora
Simon también examinó el cambio en la seguridad del cambio de revestimientos, comparando métodos convencionales lado a lado con prácticas modernas impulsadas por la automatización.
Durante el retiro de corazas tradicional, los operadores trabajan dentro del molino, eslingando manualmente las corazas hacia afuera. Este proceso de mostró en una filmación anterior, donde el revestimiento eslingado cayó desde altura sobre la carga, esquivando apenas a los trabajadores; un duro recordatorio de los riesgos involucrados.
En contraste, la última tecnología de limpieza (que RME bautizó RUSSELL Claw) recoge de manera seguras el revestimiento y lo lleva hacia el carro portacorazas, eliminando la necesidad de que el personal trabaje sobre la carga eslingando los revestimientos manualmente. Los beneficios en seguridad son medibles. Al analizar las horas-hombre de exposición al peligro por cambio de revestimientos, la automatización la ha reducido un 80% en una compañía minera.
"Si bien las prácticas tradicionales se consideraban las mejores en su época, han implicado casi seis veces el grado de exposición al riesgo en comparación con el proceso avanzado de hoy en día".
RME también deja claro que esta tecnología puede brindar un aumento de la seguridad considerable sin que sea necesaria una máquina para reemplazar corazas o un sistema de botado automatizado. Como resultado, se puede adaptar a la mayoría de las Máquinas para Revestir Molinos RUSSELL de 7 y 8 ejes en operación, garantizando accesibilidad y asequibilidad para los molinos de todos los tamaños, incluyendo operaciones, grandes, medianas y pequeñas, así como también compañías brownfield y greenfield. Regístrese aquí para descargar un estudio de caso acerca de su impacto en Minera Escondida.
Cómo la automatización desbloquea nuevos niveles de productividad
Más allá de la seguridad, la automatización es un impulsor clave de la eficiencia, optimizando movimientos multifuncionales y preprogramados a través de rutas y secuencias para acortar los tiempos de los cambios de revestimientos y mejorar la disponibilidad del molino.
Las manipuladoras de revestimientos normalmente cuentan con siete u ocho ejes de movimiento, que permiten una instalación precisa y flexible de las corazas. Manualmente, este proceso requiere una coordinación cuidadosa, por lo que está limitada por la competencia del operador. La automatización sincroniza todas las funciones disponibles, permitiendo que la manipulación y el posicionamiento de los revestimientos sean más rápidos.
"Puesto que el personal se saca del molino, podemos aumentar la velocidad de las funciones, permitiendo que la máquina opere a su rendimiento óptimo. Y no lo olvidemos, es un robot. No experimenta fatiga, solo regularidad y repetibilidad".
Simon destacó un estudio de caso que demostró las mejoras considerables en velocidad de las actividades del exterior del molino logradas mediante la automatización, destacando un aumento del 75% en la velocidad de movimiento del martillo en comparación con los métodos convencionales que dependen de un sistema de suspensión mediante jib y múltiples miembros de la cuadrilla guiando el martillo.
"La tecnología de suspensión y posicionamiento (del THUNDERBOLT SKYWAY) permite que el martillo sin culatazo bote perno tras perno. Es una secuencia simple y fluida. Es hermoso verla".
RME destaca que los sistemas de suspensión en altura que automatizan las herramientas en el exterior del molino pueden ofrecer ventajas para compañías mientras con espacio limitado en la losa y mayor flexibilidad para acceder al sistema del molino y de transmisión durante las detenciones para otras actividades planificadas de mantenimiento.
¿Qué es lo que sigue para la automatización del cambio de revestimientos del molino?
A medida que aumenta la adopción de la automatización, las expectativas de la industria en materia de funcionalidad y eficiencia siguen aumentando. Los revestimientos compuestos, particularmente en Sudamérica, están remodelando los requerimientos de herramientas, mientras que una mayor automatización indica que los usuarios esperan capacidades aumentadas de sus inversiones en tecnología.
Para cumplir con esta demanda, RME destacó su módulo del THUNDERBOLT Torquer para SKYWAY y SKYPORT, que automatiza más actividades del cambio de revestimientos en el exterior del molino.
"El Torquer ahora permite un retiro más rápido de los pernos. Además, es versátil, ya que manipula pernos doblados y reduce la necesidad de realizar trabajos en caliente de alto riesgo. También puede empujar corazas hacia el molino, sin que sea necesario un cambio de las herramientas del martillo. Y puede volver a instalar los pernos con el torque preciso, haciendo seguimiento de los valores de torqueo para minimizar el riesgo de falla de los pernos, todo mientras eliminan la manipulación manual y mejoran los resultados en seguridad".
La automatización supera las dudas del cambio de revestimientos mediante una mejora del rendimiento
En las conferencias de procesamiento de minerales recientes, los expertos en conminución han explorado más en profundidad cómo aumentar la frecuencia de los cambios de revestimientos puede mejorar el rendimiento de la planta concentradora.
Simon Thompson citó un ejemplo de una minera de oro de Australia Occidental, que extendió su calendario de reemplazo de corazas de cuatro a seis meses, pese a saber que su rendimiento era mejor a los cuatro meses, preguntándose "¿Por qué lo hacemos así? ¿Por qué empujamos la vida útil de las corazas hasta el punto en que el rendimiento disminuye?".
"Yo creo que es en parte porque le tememos al cambio de revestimientos. Tememos los riesgos en seguridad. Tenemos los riesgos de producción de una cambio de revestimientos por debajo de lo ideal. Pero cuando automatizamos las tareas del cambio de revestimientos, eliminamos estas preocupaciones. Podemos mejorar la seguridad. Podemos, ciertamente, mejorar la velocidad del cambio de revestimientos. Y podemos aumentar el rendimiento".
Múltiples estudios han mostrado que integrar corazas optimizadas para rendir con cambios de revestimientos más frecuentes, rápidos y seguros, posibles gracias a los métodos avanzados de hoy en día, permite que los operadores de los molinos eliminen las fases de bajo rendimiento del molino al comienzo y al final del ciclo de vida de los revestimientos, lo que impulsa un rendimiento más alto mientras, al mismo tiempo, optimiza las eficiencias energéticas. Lea nuestro reciente artículo de blog para revisar esta investigación y conocer más acerca del cambio de revestimientos con rendimiento optimizado.
Vea la presentación completa de Simon Thompson en la GRX25
Para explorar estas perspectivas más profundamente y comprender los resultados comerciales que las compañías mineras están logrando, incluyendo por dónde es mejor comenzar la travesía hacia el cambio de revestimientos automatizado, vea la presentación de Simon Thompson durante la GRX25 haciendo clic en la miniatura en la parte superior.
Mayor información
Contacte a RME para explorar cómo la Tecnología Avanzada de RME puede beneficiar a su compañía minera.
También puede registrarse para descargar el artículo que inspiró esta presentación: Automatización del cambio de revestimientos del molino: aplicando las lecciones aprendidas, escrito por: S. Gwynn-Jones¹, T. A. Ogden², J. Bohórquez³, D. Sims⁴, M. Turner⁵, C. Kramer⁶, y S. Smith⁷.
Si desea conversar con un experto en aplicaciones acerca de la Tecnología Avanzada de RME, contacte a RME.
CONTINÚE PARA EXPLORAR LA TECNOLOGÍA AVANZADA DE RME
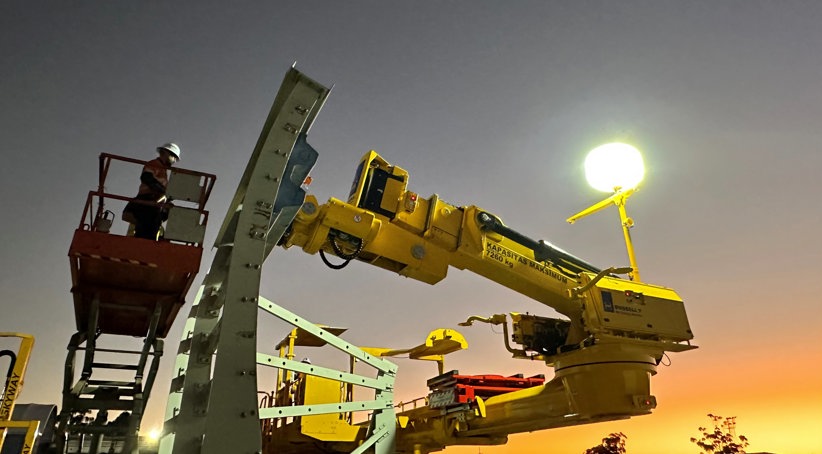
TECNOLOGÍAS AVANZADAS DE RME
Nuestra incesante búsqueda para mejorar la seguridad y la productividad nos ha llevado a desarrollar un futuro donde el cambio de revestimientos se realice desde el exterior del molino, a velocidad aún más rápidas que antes.
Más información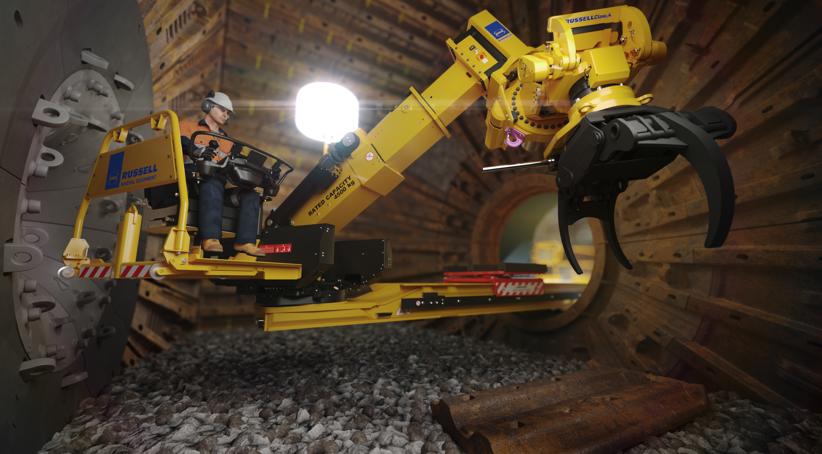
RUSSELL CLAW
Presentamos la RUSSELL Claw, la nueva herramienta experta en limpieza y eliminación del eslingado manual de revestimientos.
Capacidad de izaje hasta 8000 kg.